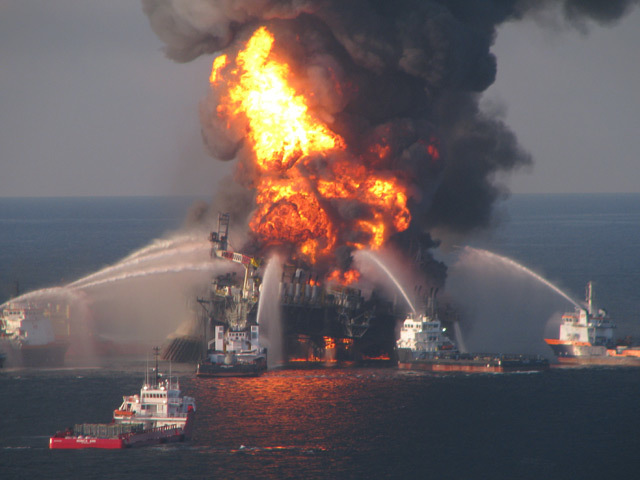
“In many ways, telling people what my job is about is straightforward”, the young safety engineer told me. “Process safety, when it comes down to it, is all about keeping the harmful stuff away from where it would do harm. However, explaining what that means I do on a day-to-day basis, that’s another matter entirely…..”
We work in complex industries, in my case, the upstream oil and gas production business.
It doesn’t take much explaining to let people know what happens when it goes wrong: the “person on the street” will be aware of Deepwater Horizon, of Piper Alpha, of Buncefield, of Texas City, of Chernobyl. Explaining all we do to stop that from happening again is not that easy, and most people aren’t that interested anyway – the tendency is to assume that the “experts” in the background are making it all work, park it and get on with day-to-day living.
But what about those whose day-to-day living includes the results of how we manage that risk?
All we do is underpinned in the UK (and many other jurisdictions) by the marvellously British concept of ALARP – making risk “as low as reasonably practicable”; it’s not enough that you show that you’ve followed a particular design method, or operate your plant in line with some good practice; you’ve got to be able to explain why the risk has been reduced to as low as you reasonably can. In a world where somehow people seem to expect that there are right and wrong answers, we live in the land of the “grey area”. And our workers on site, be that offshore and onshore, live in that land with us, right at the front line.
As technical specialists, we need to move to being technical explainers. Lee LeFever, in his book “The Art of Explanation”, captures it well. As he puts it, “You work inside a bubble. Remember that your explanation has to make sense outside of it”. We’re dealing with complex balances, trying to keep our businesses in business, while keeping safety as a core value, meeting targets, keeping people happy. No one would deliberately endanger someone’s life, but could still consider extending a maintenance interval or spending a little less here and there, that could have that very effect.
We owe it to those people who are impacted by our technical effort, directly and indirectly, to do what we can to explain why the risk they face is under control and that we have done everything that is reasonable and practicable to reduce the risk. We’ve evolved a complex ecosystem of risk assessment, hazard identification, technical evaluation, performance standards, which are intended to cover risk management. We have safe ways of working, and work within management systems that are intended to make that risk management work in practice. Our Safety Case is meant to be that explanation.
So, can we do it? From the small design choice to the full operation, we are legally obliged to be able to demonstrate the risk is ALARP. Could we explain it to the man on the site?
If we can’t, then I don’t fancy our chances of explaining it to a judge.
Conor Crowley is the consultancy director of process safety for Atkins’ Oil and Gas business. He currently leading Atkins’ Process Safety Team based in Aberdeen and is a fellow of the Institution of Chemical Engineers.
Recommended for you
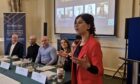