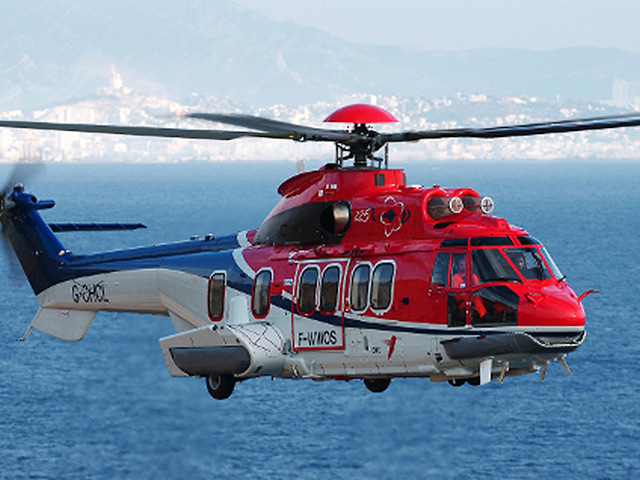
More strides are being made to make North Sea commuting safer for passengers and pilots alike.
“There is a flight manual,” says Mickael Melaye of Airbus Helicopters. “There was always a flight manual, there will always be a flight manual. But that flight manual was describing the system . . . what the system was capable of from a technical aspect.”
That is very different to the recently introduced FCOM (Flight Crew Operations Manual) for North Sea Airbus helicopter pilots, which is of course a source document, but with a big twist.
Importantly, what it does is help enable pilots to get the safe best out of the machines they fly offshore.
One of the critics of the alleged past lack of cockpit manuals in offshore helicopter aviation had been Gretchen Haskins, the CEO of the safety-focused trade grouping HeliOffshore.
But, in March, she took her hat off to Airbus for its work on developing FCOM.
She said in a statement at the time: “This work will help to optimise global operating procedures and can be used to improve training for our crews. Working in partnership, we can deliver significant safety benefits for the frontline.”
Airbus Helicopters’ head of sales promotion, Melaye, said the nature of the offshore business, coupled with statutory bodies like the European Aviation Safety Agency (EASA), UK Civil Aviation Authority and the Air Accidents Investigation Branch (AAIB) meant it had been possible to discover in an open manner what are the best practices, what is good, what is not so good, and how to make it all come together.
“The principle is dead easy; its best practice sharing; to make sure that across the board, everybody understands exactly what the system is capable of and how to make the best use of it,” Melaye told Energy.
“We started to work on this a bit more than two years ago. Version one has been introduced and version two is being introduced mid-year (about now), It’s in use already.
“It has been trialled in the North Sea with the big three operators Bond, Bristow and CHC.”
First aircraft class to be fitted with FCOM is the H225 (formerly EC225) for the simple reason that it is the most advanced in terms of avionics and level of automation. All 49 units in North Sea service have been fitted.
But what is the position with other older aircraft that today come under the Airbus wing, that is, the heritage Eurocopter fleet?
In a nutshell, Airbus Helicopters will not formally confirm a deadline against which to commit to completed FCOMs for the in-production aircraft.
The H175 is planned to be completed by the end of this year and the FCOM for the upgraded version of the H225 is the next edition planned to be produced.
A shorter version of the FCOM, a Flight Operations Briefing Notes, focusing on the autopilot, will be released for the North Sea SuperPumas, as a full FCOM is not required in line with customer requirements.
Melaye: “That’s the target; but we had to start somewhere. The 225, being the smartest aircraft we have at present in the North Sea was a good starting point.”
He applauded the feedback thus far from pilots and said that FCOM would, in essence, become organic, updating as necessary over time.
“It’s a living document. We can’t pretend that it’s OK, job done, that’s it. There could be all sorts of changes into the future, all of which will have to be taken account of.
“The next one to get FCOM will be the H175, because it too is an advanced aircraft, plus we want to make sure that its entry into service is done the best way with the best practices applied from the start. There are two EC175 aircraft in service, both flying from Den Helder.”
Two of the other critical aspects of North Sea helicopter safety being worked on at Airbus and which reach beyond the CAP 1145 recommendations issued by the CAA are to do with spatial awareness . . . knowing precisely where you, the pilots, are and where you are headed with your aircraft.
One is the drive to eliminate dependence on ground sources for information regarding flight path. It’s dead easy around airports like Aberdeen. Pilots and their aircraft are cradled in a perfectly controlled environment. Not so offshore or most places between.
“Go offshore and suddenly, not only is everything is not controlled, the environment is dynamic. Things move,” says Melaye. “You can build a picture of what’s going on out there and, 10 minutes later, it’s changed.”
“We wanted to bring safety across the board. It’s not ground dependent; the systems are on-board the aircraft.”
Airbus decided to tap its huge military helicopters experience and draw from the shipping industry. The critical addition to the sophisticated everything else available to pilots in the cockpit is AIS (Automatic Identification System).
AIS uses transponders that operate in the VHF maritime band. It is capable of communicating ship to ship as well as ship to shore, transmitting information relating to ship identification, geographic location, vessel type, and cargo information – all on a real-time, wholly automated basis.
It has been used aboard SAR helicopters “at the back” for several years; now Airbus is putting it in the cockpit; integrating it into the avionics.
“We believe that it can now bring value to the overall situation awareness of the crew,” says Melaye. “But it was quite a challenge to tie it into the existing avionics; to enable it to be useful to the crew, not as a standalone but integrated.
“On top of that there is GPS (Global Positioning System) plus the classic NDB (non-directional beacon) that we still have offshore; so you have information of where the installation is.
“If you go higher to what is going on in the air, for clouds you have radar and for traffic aircraft you have the TCAS (traffic collision avoidance system) that we now call the TCAS2. TCAS2 for Airbus is coupled to the autopilot.”
It adds up to airliner quality safety coverage and control. Including, if the aircraft systems detect a flying object on a collision trajectory then the autopilot will fly an avoiding action compliant with air traffic control regulations. The crew has two options; let the autopilot do its job, or they take direct control.
The equipment is smarter still in that the pilot can “zoom ahead” to build a picture after take-off, not just of the flight path but the destination platform or rig and locations of any nearby vessels, thanks to their AIS beacons.
“That’s not only you being prepared ahead of arrival, but being aware of what is actually happening early on rather than from say 60 nautical miles out, says Melaye.
So finally to the so-called ‘Flyaround”. Normally, a chopper takes off, bound for an offshore platform, The pilots take the aircraft to service altitude, set the course, hand over to the autopilot and, an hour or three later, start the descent manually.
Simplistically, what Airbus has sought to do is automate the approach process by smoothing the descent but with regular checks and balances throughout the process.
“The only action the crew will then have to perform is confirm the altitude to which they are going to descend. The system is going to propose then on what we call the Alt Required,” says Melaye.
“Descent will be in stages. The system proposes but the crew is kept in the loop of that decision making.
“Final landing? Two options: classic in the North Sea . . . you can’t see the deck. You will just have to press the go around and the aircraft, still on the same line, will go around.
“Similar scenario, you will see the deck, then you will stay on the four axes autopilot; you turn to the deck; use all the capabilities of the autopilot to position to the edge of the deck. Only the last few seconds are flown manually.”
Simple! Well maybe not, but it’s where North Sea helicopter transportation is headed. And that’s good.
Recommended for you
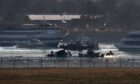