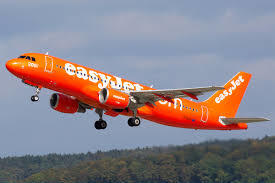
The oil and gas sector must get used to taking the “Easyjet” option for North Sea projects if it is to cut costs to a sustainable level, according to a senior supply chain executive.
Amec’s Craig Shanaghey, asset support, late life and decommissioning operations Director for Amec Foster Wheeler, said the no-frills budget airline approach to getting to a destination provided a good example of stripping out the “value-add” items that have contributed to North Sea oil lifting costs being some of most expensive in the world.
He said too many in the industry were still looking at “business class” solutions that were much more costly and were not essential to getting the job done.
“The industry is still booking the in-flight meals, the leg space and the extra baggage allowance and the free drink, if you like.
He added: “We need to get to the Easyjet model where all you’re getting is your flight. In instances where you want all the extras, let’s be open about what they really cost and we can make the real decision on whether they are really needed.”
“For me, it’s all about value, not cost. Sometimes we want to pay a bit extra if we want something to last 25-23 years, but if the platform is going to be decommissioned in five years, do we really need to be super duper pipework in there? Do we really need pipe support that can hold up the Queen Mary?
Shanaghey, who was speaking at the inaugural Topside UK conference, which examines how to extend the life of the North Sea’s ageing topside installations.
The conference’s opening session discussed the existing topsides infrastructure, number of ageing topsides assets and continued investment required to keep the North Sea industry economically viable against a backdrop where the industry is being urged to cut production costs to less than $15 a barrel to be competitive.
Oil and Gas Authority (OGA) chief executive Andy Samuel recently called for firms to go “further and faster” to do more to bring down production costs – challenging them to get below the industry body’s target of $15 per barrel.
Shanaghey said: “To get to $15 dollar lifting cost one of the key things we must do is to ask the customer,’What is it you really want?’ We need to do away over specification. There is industry available standards that are absolutely fit for purpose, but cost and complication is added on to them because of processes and procedures that demand that.
“It requires operators being really clear on what they want, and then letting the supply chain come up with a really efficient way of delivering what they want.”
Shanaghey said: “Whatever we do, needs to be sustainable. The prize for me has got to be the sustainability of the industry.
“The current industry position is that everyone is fighting for survival.
“At Amec Foster Wheeler we have the ‘More for Less’ ethos, that’s all about how we deliver efficiently and deliver to purpose.
“If a deliverable doesn’t help you build, buy or assure, you don’t need it. We’re using that to get efficiency and scalability on how we deliver, with no compromise to safety and integrity.
“The most important thing is transformational change, that’s how we working conjunction across the supply chain – operators, tier 1 contractors and tier 2 contractors and supply companies – working together and trusting each other to get the job done.”
Topsides UK 2016 Conference and Exhibition, focusing on the late life of maturing topsides installations, is the first event of its kind in Europe.
Recommended for you
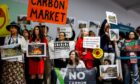