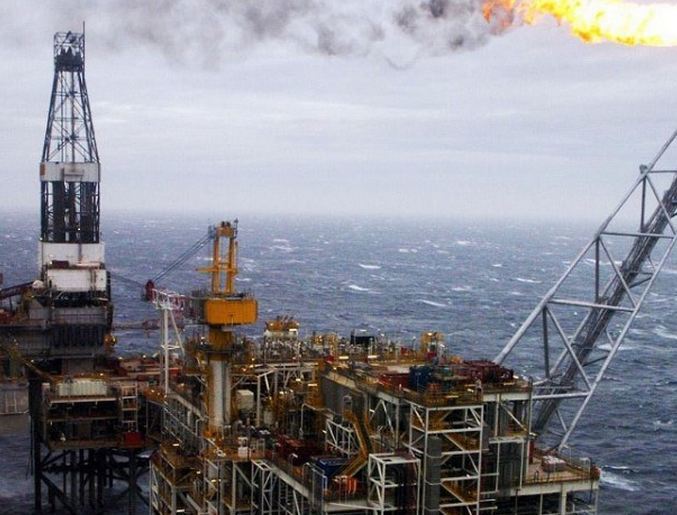
Energy Voice has teamed up with Shell to celebrate 40 years of Brent. This promoted series will examine the people, milestones and technology that helped make this historic North Sea find possible. It will also analyse what lies ahead for the breakthrough discovery. Happy 40th Brent!
So what were, or indeed are, the key technology milestones attributable to Brent?
“Leaving aside the platforms, if you just think about Brent in terms of some of the wells technologies that were tried, proven and used on Brent for the redevelopment to enable the gas cap blow-down, that was a huge milestone,” says UK & Ireland upstream VP, Paul Goodfellow.
“A lot of the infrastructure technologies in terms of how Brent was connected to other North Sea production infrastructure is effectively another milestone.
“For me it’s not one of those projects where there has been a whole series of incremental breakthroughs to enhance production, make it work better.
“It’s that sort of mindset that takes you from a design-life of 25 years to being here 40 years later (anniversary date is November 10) with Brent still producing, albeit at a very different level to the 1980s heyday.”
When Brent was first developed, what was the recovery rate expectation?
“The easiest way to think about that is to say, well, we expected Brent to produce for 25 years, not the 40 years achieved thus far,” says Goodfellow.
“So, without getting into the science of recovery factors; that to me is the easiest way to think about it.
“As you would expect during the life of a field, as a result of additional seismic and reservoir modelling, you find new production to bring on and it is that, coupled with advances in technology, which more than anything else enabled the additional 15 years of production.
“That’s the same for many oil & gas fields. Good fields tend to become great fields. Brent is an example.”
As of today roughly, what is the estimated recovery factor? Shell has recovered just over 3billion barrels oil equivalent of which 2billion is oil, according to a North Sea recovery factors presentation by Mike Shepherd.
In percentage terms, that’s around 80% of the gas originally in place and 53% of the oil.
By comparison, the oil recovery factor for Forties thus far is 61% – 2.74billion barrels – bearing in mind that the field is still producing significantly. The average recovery factor is 22% worldwide.
Goodfellow: “We think that, by the time we get through to Brent Charlie, we will have produced in the upper 90% range of the recovery gas volume that was once there.”
In short, this is positive proof that the bold champagne cork reservoir depressurisation model behind the Brent redevelopment in the 1990s was on the mark.
“It’s delivered hugely positive impacts, not least in terms of jobs, the supply chain and tax to the Treasury.
“Moreover, what the service sector learned from that project has helped to build the industry that we have here today.
“Remember, it’s important to look at Brent in the broader context and not just what the Shell/Esso JV has recovered from the field.”
Indeed, the gas cap project took place against the backdrop of the UK offshore industry’s CRINE cost-cutting drive, where the supply chain was actively pumped for ideas by operators via various sub-initiatives, including risk-based gain-sharing agreements. Shell was an active participant.
“And that sort of thing is going on today …the collaborative approach and how to pull in ideas from the supply side to help augment the ideas generated internally by the operators,” says Goodfellow.
“When you look at the decommissioning side and the study-work and thinking that have been going on around that, that’s absolutely applicable there as well.
“More so than ever as an industry, as a country, we need differentiated thinking about how to decommission the infrastructure that’s out there.”
According to Brent decom manager Duncan Manning, there are a number of evolutionary and revolutionary changes in technology that have happened over the last 10 years that have benefitted Brent in the long march to cessation of production.
“From an evolutionary perspective, clearly the ability to abandon wells has incrementally improved and delivered efficiencies in terms of reservoir isolation,” says Manning.
“It doesn’t attract attention, mostly because it is out of sight and out of mind but, actually, the biggest cost element of decom is reservoir isolation. Incremental changes have collectively had an exponential effect on the cost of this.”
And what about the fact that a lot of wells are decommissioned on the UKCS, but now the industry is having “ah but” moments about the way this is being done with research commissioned through ITF (Industry Technology Facilitator).
“I’m not sure about doubts. We’re about halfway through the Brent well-stock and have experienced a number of lessons early on.
“We’re on a learning curve where we’re now driving really good performance with regard to well abandonment delivery, making sure there is alignment on the platforms between the operations teams and the wells teams; but also using technology to drive ever-increasing efficiency of delivery as well.”
Well-related technologies are regarded by Manning as evolutionary. But opting for the massive heavy lifter cum pipelayer Pioneering Spirit to take 24,000 tonne platform topsides off in one go is revolutionary.
“Allseas have been speaking with Shell about it for a number of years,” says Manning. “Though we had looked at more traditional methods of reverse installation.”
So what swung it?
“We needed to assure ourselves that this technology was in fact workable. We needed to do the technical assurance to reassure ourselves that we would be signing up to a contract that the ship was actually capable of delivering to.
“Also, this was against a backdrop of heavy-lift vessels that have a long history of both install and reverse install track record.”
What, if any, influence did Shell have on the design of the Allseas vessel?
In short, Shell worked closely with Allseas in delivering the overall capability of lifting a large topsides in a single lift and how such topsides would cope with something they were never designed for.
Also, there was the issue of how the recycling would be carried out, ergo making sure that the recipient recycling yard would be fit and capable of handling a skid with 24,500 tonnes of Brent
Delta topsides sat on it. In short, would Able’s quayside at Teesside be strong enough?
Its striking that there now exists a vessel that can lift off the topsides of a large platform in one go, rather than resorting to removal of modules one-by-one for breaking up onshore or piece small and chopping up steelwork in-situ, prior to delivering ashore for recycling.
Manning: “There are a number of attractions in the heavy-lift option. When we signed the contract in 2013, very much at the front of our mind was, of course, the contract itself.
“But also at that time we had estimated that it would remove around one million man-hours of offshore work with all the complexity that it involves, and move the dismantling ashore to a more controlled environment where time and weather are less significant factors.”
So, even if the cost ends up being around the same as for decommissioning platforms in-situ, does this mean that Shell would still be satisfied with the decision to use Pioneering Spirit?
Goodfellow responds: “When we went out to the market in 2012/13, it looked as if the (existing) heavy lifters would be busy for years ahead.
“It’s like all of these things. This decision represents a continuum of thinking in terms of what the available options could be.”
To celebrate and capture the rich history of Brent, Shell is commissioning an e-memory book and an oral history project. If you have an unforgettable Brent story, or have an old photo or memory you would like to share, you can submit them at www.shell.co.uk/brentmemories. The oral history project will be interviewing a selection of candidates from a variety of roles and years to record the highlights and uncover the less widely known stories from the last 40 years. Digital recordings will be donated to The University of Aberdeen who will share these stories with anyone who is interested, from family members and researchers, to students and the public. Please contact Brentinfo@shell.com if you would like more information about these projects.
Recommended for you
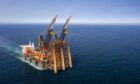