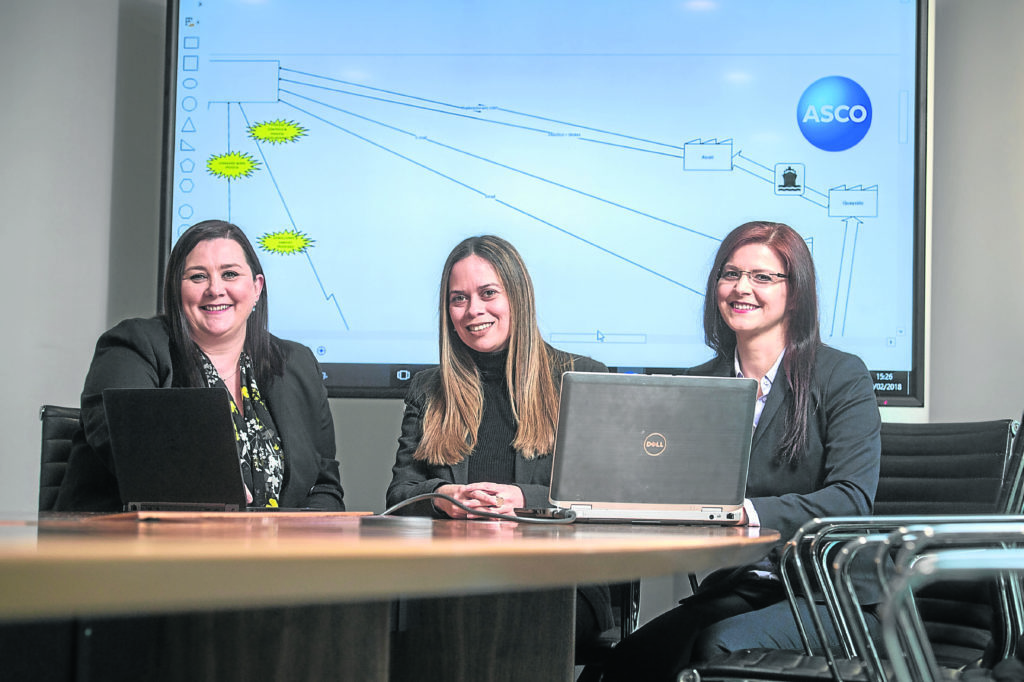
Around one-third of lost time offshore can be attributed to materials – for example, equipment being inaccessible when required. While costs remain higher in the North Sea than in equivalent mature basins, this is something industry must action.
One group of talented female professionals at global materials management specialist ASCO is striving to address this imbalance and ‘fix’ the business architecture around offshore operations to help sustain the North Sea as a viable, long-term and competitive environment.
By deploying lean methodology, innovative systems and leveraging data analytics, the business is working with operators to reduce waste and transform efficiency of processes at the heart of the oil and gas industry.
The company’s dedicated Master Lean Six Sigma coach, Henrietta Pallos, is responsible for introducing Lean Six Sigma process improvement methodology which is centred around clients’ business needs and continuous improvement. Suhail Diaz Valderamma is the project manager leading a significant overhaul of an oil major’s materials management operations. Finally, Angela Milne is the business architect and project manager currently undertaking her 12th different business implementation assignment; utilising her 20-plus years’ industry experience.
Working alongside ASCO’s director of warehousing and inventory, Allan Scott, this trio is on a mission to bring a strategic focus to inventory and materials and transform clients’ supply chain practices.
Henrietta said: “To ensure the North Sea is a competitive basin, enhance production efficiency and achieve significant improvement, we need to understand, control and simplify processes before automating them, and through this journey eliminate value leakage throughout the entire supply chain.
“We begin by mapping out each customer journey from a process and technology perspective; studying and analysing their business to identify actual needs, beyond their stated requirements. By establishing overall strategy and objectives for the next few years, we can then align processes towards the pursuit of that goal.”
At the heart of ASCO’s approach lies a focus on first delivering the necessary underlying process improvements before augmenting those changes in a meaningful way with the right technologies and systems.
Suhail explained: “There is an opportunity to better track equipment coming on and offshore, not least how and when it’s being utilised. Part of our solution simplifies that process and creates a benchmark that captures knowledge and best practice from other industries, such as retail and automotive.
“By digitalising the end-to-end supply chain, we can track and trace all items to the point of consumption much more effectively through the use of technology.”
Angela added: “We’re on a mission to transform the way industry works.
“But it’s not being done in isolation: we’ve taken a highly collaborative approach that involves getting buy-in from clients and cherry-picking examples of best practice from across diverse companies and sectors to benefit the industry as a whole.
“In the next few months, we will deploy a retail logistics model for a major operator and show that supply chain transformation is possible.
“Through greater standardisation and development of people across the industry, we can achieve a coherent way of getting everyone within an organisation – including disparate contractors who have previously been neglected in terms of professional development – pulling in the same direction.
“Clearly, these changes aren’t going to happen overnight, but – given the right support – we strongly feel that their potential effects will be far-reaching in terms of upskilling people, changing behaviours, embedding sustainability and supporting the industry in delivering its vision of a digitally enabled supply chain.”
Over the past 50 years, ASCO has continued to build upon the foundations of the North Sea’s oil and gas industry.
Now, the valuable process improvement work started by Henrietta, Suhail, Angela and the rest of their team in Aberdeen is expected to be rolled out across the company’s other global operations; again, showcasing the North Sea as a global benchmark for excellence.
Recommended for you
