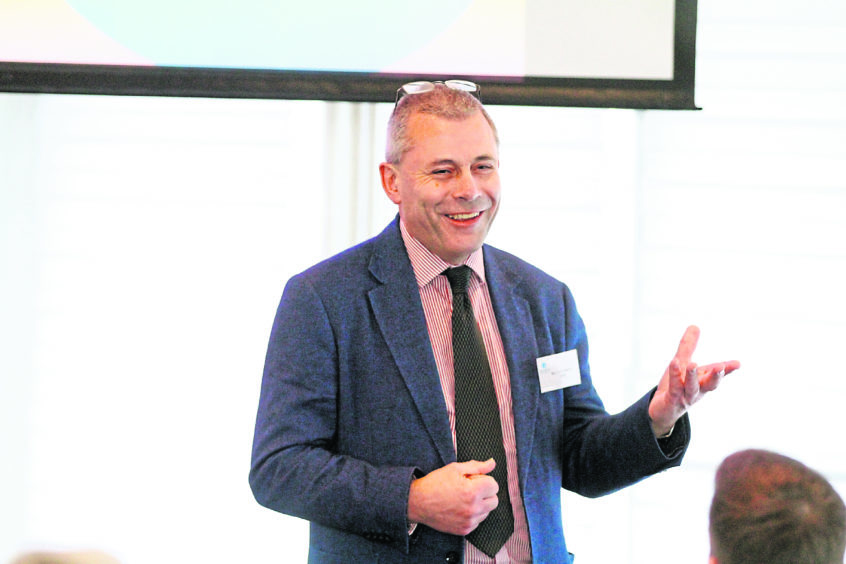
North Sea operators must treat oilfield service (OFS) firms with care or they could end up becoming “second-class clients” in a tightening market, an industry figure has said.
Bill Cattanach, head of supply chain at the Oil and Gas Authority (OGA), said the OFS sector “almost lost a generation of workers” due to redundancies and the scrapping of apprenticeships during the downturn.
With offshore activity expected to pick up, suppliers with smaller headcounts and fewer resources could find it difficult to keep up with the pace.
It means OFS companies whose services and products are in the most demand will have to prioritise even more wisely which jobs they take on and in what sequence.
If operators are not in the good books, they may find themselves down the pecking order, waiting in line.
That would put the shoe on the other foot, in a period when suppliers’ prices have been squeezed.
That stage has not been reached and, with solid planning and continued collaboration, bottlenecks can be managed.
Now for some sobering stats. At its peak in 2014, the UK oil and gas industry supported 460,000 jobs through direct and indirect employment and positions that are sustained by the sector’s wider economic contribution.
That headline figure has since shrunk to 280,000, while direct employment sank to 28,300 in 2017 from 41,300 in 2014, according to Oil and Gas UK’s economic reports for the last two years.
About 80% of people who work in the industry are in the supply chain. That is where many of the redundancies would have been felt after activity levels fell off a cliff in 2014.
Mr Cattanach is sure workforce numbers will not go back to 2014 levels.
Furthermore, a lot of the people who join the sector in the coming years will be different to what came before.
A report by Opito and Robert Gordon University said the UK oil industry would have to hire more than 40,000 people from 2018-35.
Of that number, 10,000 will be in roles that don’t currently exist, in areas such as data science, robotics, material science, nano-technology and cyber security.
Mr Cattanach said the industry would need “fewer people and different people”.
He said redesigning existing platforms and kitting them out with sensors so they can be de-manned and operated from shore was “the future”.
He believes Aker BP set a positive example earlier this year when it became the first company on the Norwegian Continental Shelf to operate a manned platform from an onshore control room.
Ivar Aasen in the North Sea is now run from offices in Trondheim.
While job losses are always bitterly regrettable, Mr Cattanach believes the downturn was the “catalyst that sparked changes” which needed to happen.
He acknowledged the industry’s costs were “out of control” and had to be brought “back into line”.
Since then, the North Sea oil and gas sector has become far more efficient and competitive in comparison with other regions.
Production efficiency has reached 74%, its highest level for a decade, while unit operating costs halved between 2014-16 and have stabilised at around $15-16 per barrel of oil equivalent, OGUK said in its latest business outlook report.
Production has increased or stayed flat every year since 2014 and the OGA has raised its estimates for output between 2016-50 to 11.9 billion barrels, which is 3.9bn higher than the prediction made in March 2015.
However, turnover for the UK OFS sector dropped 9% to £26.9bn in 2017, marking a third consecutive year of decline, while earnings plunged 31% to £1.78bn, according to a recent study by EY.
Derek Leith, EY partner and head of oil and gas tax, said it was “not unusual” for OFS companies to take longer to recover than exploration and production (E&P) businesses, which started posting hefty profits during the last two years.
Mr Leith believes the OFS sector “most probably” came through the bottom of the down-cycle in 2017 and spotted some positive signs last year.
At least 17 new North Sea developments were approved last year, which should generate around £3.7bn-worth of investment, compared to around seven project sanctions in 2017, EY said.
The word collaboration has been kicked around a lot, but Mr Cattanach said several projects which came on stream in recent years would have been impossible without better collaboration between operators and suppliers.
He said OFS firms had used new approaches to reduce the cost of projects.
OFS companies worked on a number of projects during the last few years on a deferred payment basis, whereby they supplied services and waited until first oil to get paid.
Other contracts have contained incentives that further benefit contractors if they help deliver projects on time and on budget.
Mr Cattanach said making the supplier a real partner in the project was key.
That means getting them involved early and openly discussing the challenges, rather than dishing out the usual invites to tender.
These approaches have created a win-win situation in which operators’ projects are delivered and suppliers avoid laying people off.
The North Sea industry has reached an important time. Mr Cattanach said: “We are seeing a real upturn coming and would need to make sure we maintain the same culture and relationship between operators and the supply chain that will ensure costs do not spiral again.”
In that regard, the OGA is doing its bit, using supply chain action plans, which need to be submitted to support operators’ field development plans and decommissioning programmes.
Their purpose is to make sure operators get their engagement with the supply chain right – and that as much value as possible is derived from project activity. More than 60 have been received since April 2018.
The action plans encourage early engagement, the adoption of innovative technology, contracting models and industry standards.
Mr Cattanach said: “You need labour on your job. The only way you will get that is through collaborative relations with the supply chain. In some areas of the supply chain there’s still overcapacity and that’s why margins are still so slim, because contractors are still competing aggressively against each other to win work.
“But there’s a thin line between overcapacity and undercapacity.
“We could quickly get to the point where there are not enough people.
“My prediction is that by 2020, people, resources and costs will be very real again, putting upward pressure on costs.”
Recommended for you
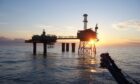