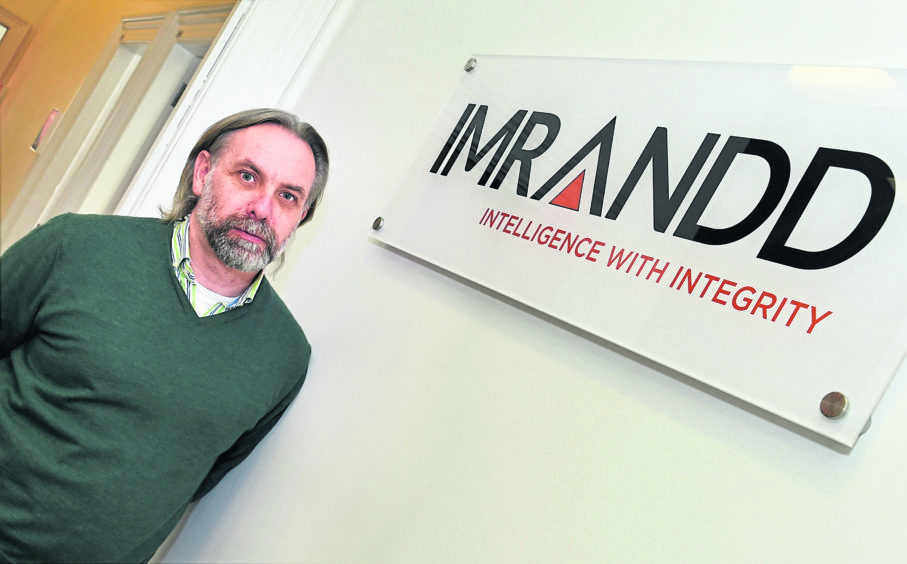
It has been a busy three years for integrity management firm Imrandd.
In its short history, the company has gone from one major client to nearly a dozen, a handful of staff to around 40 and a series of office expansions, finally taking it to its two-floor premises on Union Street in Aberdeen six months ago.
To an outsider it looks counter-intuitive. The business has managed to grow and thrive amid years which have been largely characterised by a downturn for the oil and gas industry.
But with that has come a lot of changed attitudes to the way firms do business, which managing director (or “Big Cheese”, as it says on his name badge) Innes Auchterlonie, believes played well into Imrandd’s approach.
He said: “I think it would be fair to say that if it wasn’t for the downturn we may not exist.
“It may seem like a bad time to start the business but with oil and gas companies more focused on cost and more prepared to try something different, it gave opportunities for start-ups.
“There is definitely more appetite at the moment for people to try new things. With ourselves, upwards of 25% of company effort goes into R&D so we’re constantly developing new ideas, new technology.
“We find that operators are not only accepting but are actively seeking to engage companies who are being a bit more forward-thinking and are trying new things.”
The firm, entirely self-funded by the founders, has enjoyed growth thanks to the team’s “understanding of business” and the influence of integrity management on the bottom line.
Mr Auchterlonie, who comes from an engineering background, believes integrity management should be as much a business discipline as an engineering one.
However, just because they have enjoyed success, doesn’t mean it didn’t feel like a gamble in the beginning.
“It felt hugely risky to begin with,” he said. “I quit a job with a very well-known oil and gas operator to start the company with my partners.
“To begin with, we reduced our personal income with the company, considerably from what we had before, and retained capital within the company to be able to reinvest.
“It’s that reinvestment that has allowed us to grow, but it has meant we’ve been able to do that without any external investment into the company.
“We’re conscious of the problems you can have with very rapid growth so we’ve deliberately spent a lot of time putting the business processes and infrastructure in place that will allow us to take on more work.
“Equally there has been a huge amount of effort put into finding the right people, building the right teams and systems and HR facilities that allow us to expand at the kind of rate we are.
“That has taken significant reinvestment but we’re now in a position where we can cope with significantly more growth without any further spend.”
Imrandd is primarily focused on the North Sea but also has clients in the Middle East and West Africa, and growth is what it will continue to chase after.
A heavy emphasis is placed on research and development – hence the name Imrandd (Integrity Management Research and Development).
Some of its new technologies have allowed it to help tackle some larger industry issues, particularly analysing mounds of industry data – which for some assets go back decades – and making sure that set of information is reliable.
To that end, it has developed a Deep Data Excavator – a software that can rapidly process “trapped information” that only exists in reports in varying formats and “cleanse it” into something that can be analysed.
It also has software that can filter inspection data, allowing operators to understand what is reliable and what needs further investigation.
Imrandd said this allows high-potential failures to be highlighted that may not have otherwise been spotted and result in fewer inspections needing to be carried out.
Mr Auchterlonie said: “It’s cost saving in terms of man-hours but it means tasks that were previously almost impossible are now a reality.
“For one client recently we processed 15,000 documents in a matter of days. If they were to do that manually, you’d be looking at a team of two or three people working to do the same thing which would take over a year.
“With the analytics and the data cleansing, for one asset we carried that out on there was a previous attempt by the operator to do that manually, which was abandoned after a year because it was simply taking too long.
“Our initial processing of the data, which allowed us to classify if everything was reliable or not, took 20 minutes.
“There was further manual work we had to do after that which took a matter of weeks, but the initial processing allowed them to gain confidence in their data and know whether it was flawed.
“It’s not only about cost saving, it is about safer assets as well. By understanding the degradation patterns you have a better understanding of where your failures are going to come from and what might be the underlying causes.”
Recommended for you
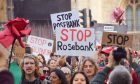