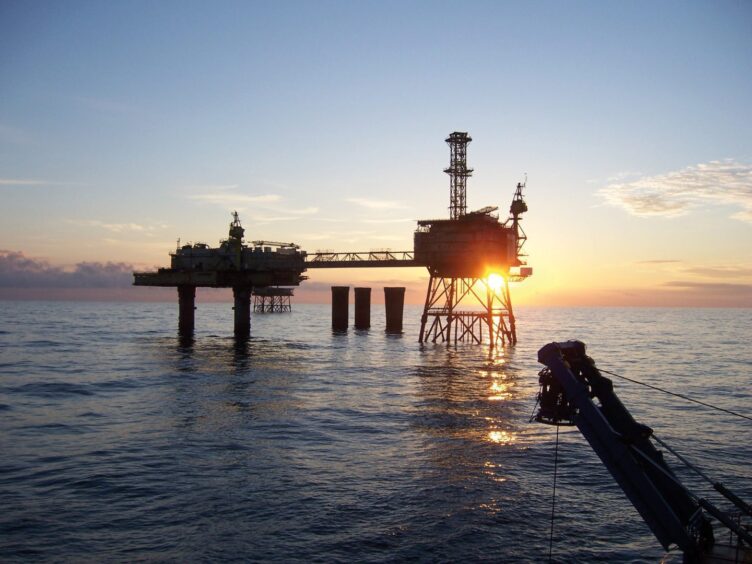
Decommissioning represents a vital transitional phase for the North Sea oil and gas industry.
As hydrocarbon production in the region wanes, and renewables are only just beginning to ramp up, decommissioning is set to provide jobs and revenues for the medium term.
Furthermore, decommissioning can set the stage for the next chapter of the North Sea, helping repurpose existing infrastructure for new projects, such as hydrogen production and carbon capture utilisation and storage, that fit in with the UK’s net-zero ambitions.
But North Sea players have been slow to decommission their operations. The North Sea Transition Authority (NSTA) claimed that while operators spent around £2bn on decommissioning in 2023, in line with forecasts, they only completed around 70% of planned well decommissioning activities.
It added that there are close to 940 inactive wells that still need to be decommissioned, of which 500 have missed their original deadline.
This has driven the body to consider naming and shaming operators who fail to meet their decommissioning deadlines.
Several reasons have been given for this slow progress. With decommissioning set to cost around £40b over the next 10-15 years, operators could be loath to commit money that won’t bring a return on investment.
Partly, there is a wait-and-see attitude as inflation leads operators to defer work as they hope costs drop and new, more effective technologies become available.
However, CEO of Aberdeen-based Raptor Data Paul McClure told Energy Voice that the delay is putting the entire region in danger, “because you risk the chance that already limited and hard to source resources and capability go away from the North Sea and don’t return.
“And then your strategy to decommission falls to pieces.”
A new approach is needed, and new technology and new solutions have a part to play in decommissioning.
NSTA decommissioning manager Alasdair Thomas has warned of a closing window to bring new technologies to market, giving them “the next five years” if they are to make a difference, especially in well plugging and abandonment.
The Net Zero Technology Centre (NZTC) has previously said that it is seeking innovations to enable rigless plug and abandonment technologies to enable faster, lower-cost trials and wider industry adoption in the UK.
The cement solution
“The industry’s doing quite well at collaborating at making the North Sea a world leader in terms of cost-effective decommissioning,” McClure said. “But there hasn’t been a revolutionary step.”
Cement is the current material of choice for plugging and abandoning a well, a long-accepted-as-proven solution. This involves removing old cement from the well bore before pumping in new cement to seal it.
“But is it the best solution? Is it the most cost-effective solution?” McClure challenged.
Despite being the go-to method, it has issues – cement can degrade over time and lead to leakage. In addition, using cement is a costly process involving spending around £1 million per day hiring a rig.
“You need to mix and pump that cement, you need to ensure that the cement is set, you need to pressure test it and you need to put weight on it to make sure it’s a robust plug,” McClure explained.
“I noticed there’s other technologies pulling through that aren’t quite there yet because there’s a gap between whether they can do the job and whether you can prove that they do the job.”
Bismuth is one such potential new technology that could replace cement. This involves using a mass of bismuth or a collection of bismuth beads. This is inserted into the well bore and ignited.
Like water, bismuth is denser as a liquid, so when the molten metal flows into any fissures or pores in the well and solidifies, it expands to form a tighter seal.
“So, instead of a rig, you just need a small intervention vessel or workover vessel,” McClure said. “You don’t need pumps, you need a wire line unit and a heater.”
Proving technology
Raptor Data has conducted work to verify the effectiveness of bismuth plug seals. Its Pathfinder product can measure wellbore pressure, temperature and provides acoustic analytics, providing crucial data on the effectiveness of a bismuth seal.
A supermajor oil and gas company was among the early backers of the firm and has deployed Raptor’s systems in a trial in Norway.
The trial meant validating the well to show that a bismuth plug is equivalent, if not better, than the standard cement plug.
“You need data to understand how the bismuth plug has been constructed, whether it’s the right length, whether it’s a tight fit and whether it’s a proper fit-for-purpose pressure seal,” McClure said, “Data is the number one priority.
“We went to a test well in Norway and demonstrated we could send signals of pressure and temperature data from below the plug to above the plug, and therefore verify that we had a pressure seal.”
But on-the-spot data is just one part of the equation. If a well is to be abandoned permanently, operators need data long after the well has been sealed.
“You need to monitor whether that plug is performing properly for a reasonable period of time and then hopefully for a lifetime,” McClure said.
“Our strategy is that we put tools in the well bore below the plug that verify the plug while you’re doing it, and then they continue to transmit data for a period of time afterwards, typically five years.
“That provides a high level of confidence that you can actually repurpose the well. You’ve got a high level of confidence that the well is robust and that the plug is performing as designed.”
The next phase
It is this long-term data that is vital to building the next stage of the North Sea industry.
Old wells can be repurposed for a variety of purposes. They can be used to pump carbon dioxide into existing reservoirs, forming the basis of carbon capture and storage projects.
For example, one company, Perenco, is looking to use an existing well to inject carbon dioxide into the existing Leman field. Projects like this would give a second life to gas fields across the North Sea.
“We’re at an inflexion point,” McClure said. “If you’re an oil company and you’ve got a hole in the ground, you’ve got a couple of choices, and the viability of those choices are changing.
“We’re seeing repurposing as a big thing – can that well be used for something else, such as a geothermal well or carbon capture and storage?
“If it’s a geothermal well or a carbon capture well, you don’t completely abandon it, but you do need to put infrastructure in the well to seal off the hydrocarbons and ensure that it’s safe.
Repurposing also helps create a better economic case for decommissioning. At present, there millions of dollars spent on sealing a well are essentially lost money – they don’t bring a return on investment like drilling the well in the first place.
“I do think that operators may be delaying decisions to see if there’s a more appropriate use of the well before they actually get rid of them,” McClure said.
“The economics don’t work right now. If you have to bring in a $1m per day rig to do that, if you can do it for a tenth of the price, then it’s a different equation.”
But by adding a potential source of revenue down the line, companies have an incentive to make a final investment decision beyond government requirements.
“Revolutionary is a strong word, but I think that’s what we need,” McClure said.
“There is a reluctance to change and the reluctance to change is associated with the risk. Nobody wants to be associated with a well that they abandoned and in two years something goes wrong.
“What we need to do as an industry is embrace the fact that there are new technologies and new techniques out there and have a journey to collect data and demonstrate to ourselves and the industry that there is a revolution coming that will enable us to do things without high level high-cost drilling rigs and at very much lower costs and very much higher efficiencies. Data and analytics is the key to delivering this.”
Recommended for you
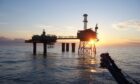