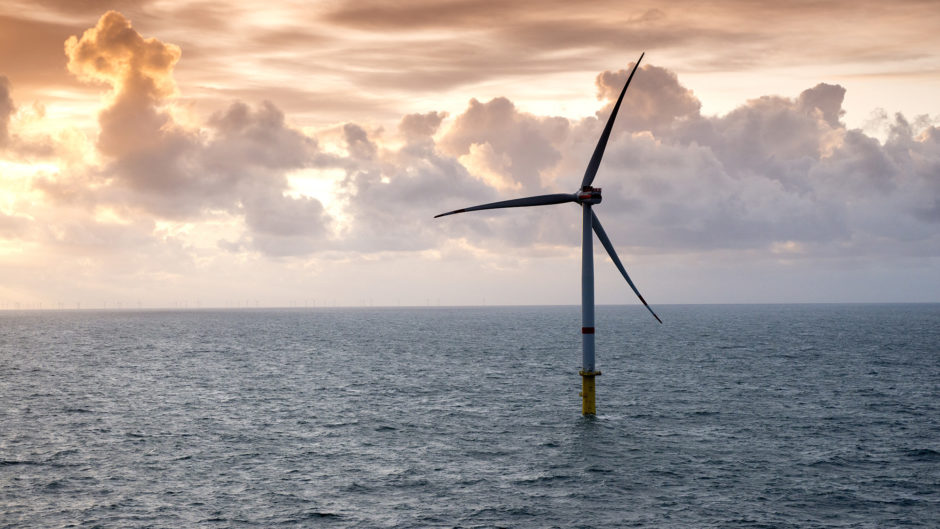
The offshore wind industry has achieved feats of engineering in recent decades that helped fuel the UK’s ambitious climate change targets.
The make-up of turbines means that they are already 85-90% recyclable, which is a good place to be, but there is a journey ahead to close the remaining gap, which, in terms of volume, is largely about the disposal of composite blades.
At-scale recycling will be a good solution, but we can also look at approaches for designing out waste from the start, extending component lifetimes and more advanced circular economy approaches (reuse, refurbishment and remanufacturing).
By 2050, the global offshore wind industry will decommission up to 85GW capacity and onshore wind will decommission another 1,200GW. That’s a huge number of wind turbines that can feed a future circular economy. If the UK can innovate these approaches and set up a circular economy first, it will reap the economic benefits of this fast-growing market.
An estimated 40,000 to 60,000 tonnes of plastic composites will reach end of life in the global wind sector by 2023 alone, largely from their blades, which are typically made of carbon or glass fibre composites.
While we have identified 14 recycling technologies that could be applied to blades, each of them comes with questions that remain to be answered in terms of the quality of recovered materials, matching recyclates to a saleable end product and their own environmental impacts.
What we’re doing
We’ve set a target of developing an at-scale demonstration of blade recycling within the next five years as part of our new Circular Economy for the Wind Sector Joint Industry Project (CEWS). The motivations are to support the offshore wind industry’s future sustainability, ensure security of supply for manufacturers (as we will arguably need recovered carbon fibres to ensure tzhe volumes of blades needed), and create new business opportunities for the UK too. We estimate that a spin-off circular economy from the wind sector (bringing in remanufacturing, refurbishment and other circular economy approaches) would create 20,000 indirect jobs from offshore wind (over and above the current target of 60,000 jobs targeted by government). Through the Energy Transition Alliance, our collaboration with OGTC, we have published a Wind Turbine Blade Recycling Report, outlining the key innovation challenges that need to be met for us to achieve this goal.
The report gives several key recommendations that support our five-year target:
Cross-sector collaboration will be critical
For composites recycling to reach the necessary economies of scale, plants will need to cater to multiple industries: blades alone will not provide a sufficient flow of material to make them commercially viable. A new collaboration SusWIND sees us join forces with both wind industry partners and research bodies with expertise in the automotive, aerospace and other sectors too. This new project will discover and demonstrate viable ways to recycle composite wind turbine blades, explore the use of sustainable materials and processes in developing composites for blades, and fuel design innovations that will future-proof the turbine blades of tomorrow. Meanwhile, Carbo4Power, a multidisciplinary team of 18 partners from eight countries, working on a four-year project, is developing a new generation of lightweight, high strength, multifunctional, digitalised multi-materials for offshore wind and tidal blades. The innovative concept is based on nano-engineered hybrid (multi)materials and their intelligent architectures.
This investment in innovation is crucial in supporting our five-year target, but it is just the start.
Creating recyclates with purpose
To have true benefit to the environment, we must look for recycling opportunities with purpose. Creating new materials from recyclates is only a solution if they will be used in end products; it is not an end in itself. Our approach to R&D in this area is to engage the entire supply chain so that we can ensure recyclates are matched to viable end products. By raising awareness of this incredible circular economy business opportunity, we can combine our drive for environmental impact with shared moves towards the growth of UK manufacturing.
Next Steps
The demand, the technology, the economic need and the environmental logic for blade recycling is abundantly clear. To meet Net Zero, wind power is key, so the number of turbines will continue to grow, but so will the size of the blades.
With this comes a need to ensure a sustainable supply of materials for manufacturing, so the sector must lead the way in making large-scale composite recycling not only viable, but a gamechanger in economic growth.
With the concerted efforts now underway, we can support the creation of thousands of new UK jobs in the coming years through the reuse and repair of components, and we can design out waste from the start, with the creation of a truly sustainable infrastructure.
Get inspired and get in touch
Watch ORE Catapult’s new film to see circular economy routes for today’s turbines, component by component
To find out how your business could join the Circular Economy in the Wind Sector JIP, contact: CIRCULAR@ore.catapult.org.uk for more information.
Peter MacDonald is head of engineering at the Offshore Renewable Energy (ORE) Catapult, the UK’s leading innovation and research centre.
Recommended for you
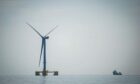