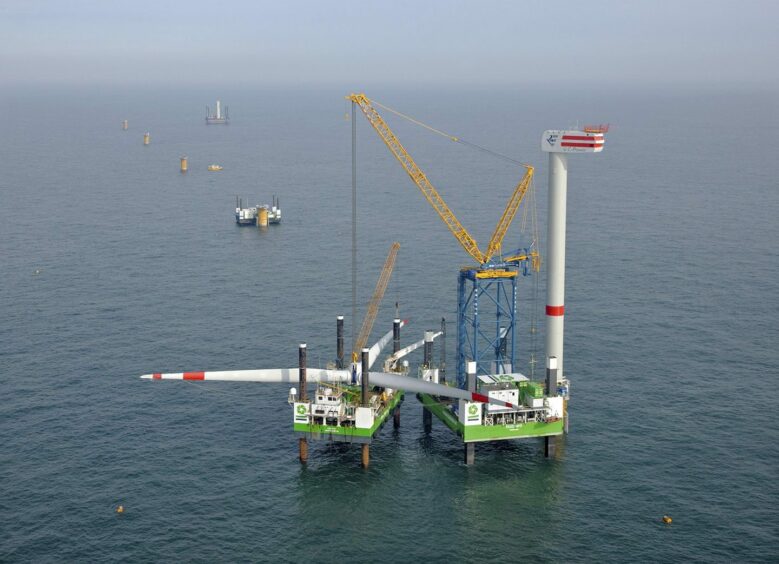
The offshore wind industry is undergoing its next big expansion. Licensing rounds are growing, interest in the new floating designs are high, and investors are active.
Exponential growth seems on the horizon. It is estimated around 20,000 turbines are needed by 2050 to meet the global target of 300GW, and the UK target for 2030 requires a five-fold increase of current capacity to 50GW, with 5GW to come from floating wind. But there remain challenges. Larger projects require port infrastructure and supply chain development and expansion to avoid bottlenecks and control manufacturing costs. Wide-ranging obstacles exist, from the manufacturing of component parts, to vessel availability for installation. Most pressingly for the UK, current industrial capacity falls short of this anticipated demand and without investment, projects will be reliant on foreign manufacturing, particularly of foundations (both fixed and floating), with the attendant increases in costs and risks in their transport. An opportunity also risks being missed for the UK to become a global leader in terms of expertise and capability.
This is a point that the UK government appears cognisant of and, indeed, future allocation rounds of CfD may include weighting for British local onshore content. The Offshore Wind Sector Deal, announced in 2019, included an industry commitment to 60% local content by 2030. The benefits of having access to such content is therefore clear and is a potential factor to be included when determining a CfD application’s outcome.
The development and use of freeports is similarly essential. These ports offer tax benefits and tariff exemptions, in particular allowing companies to import goods (including steel), convert them into final products, and then export them (by, for example, installing them in a wind farm offshore, outside national waters) without paying tariffs. They will also allow for the clustering of suppliers which will help increase economies of scale and reduce issues with transportation.
Finally, however, there is the added issue of the increased complexity of floating wind. The manufacturing and installation process varies for each substructure type (e.g. semi-sub, barge, spar and TLP). While many designs are fundamentally similar at heart, exciting and radical concepts exist which take very different approaches. Adaptability of any supply chain is therefore key.
One solution for many of these issues is being developed by one of our clients, Offshore Solutions Group (OSG), who have created a consortium of UK suppliers, sharing knowledge, innovation and developing new technology-led manufacturing capability, to facilitate such production. The linking of suppliers with facilities at a freeport, and one which is design agnostic when it comes to floating foundations, will minimise logistical challenges and allow for design development to be best suited to the final assembly site and deployment location.
Having all of the key players working together from the outset is the best way to minimise the risk of problems down the line. It also enables the development of serial production and the standardisation of processes, which is both necessary to maximise output, and to deliver ongoing cost reduction expectations. Investors and insurers will always be more comfortable with known entities and established methodologies. OSG also intend to incorporate training and development programs, to help establish a world-class pool of talent with the UK. This will create something of a virtuous circle, whereby the increasing skill and capability in the UK helps to increase the demand for such local content, thereby delivering increased experience and increased productivity.
In simple terms, while diving in to the offshore wind market alone can seem intimidating, the benefits of working with an existing team such as OSG could be significant.
Recommended for you
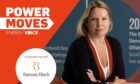