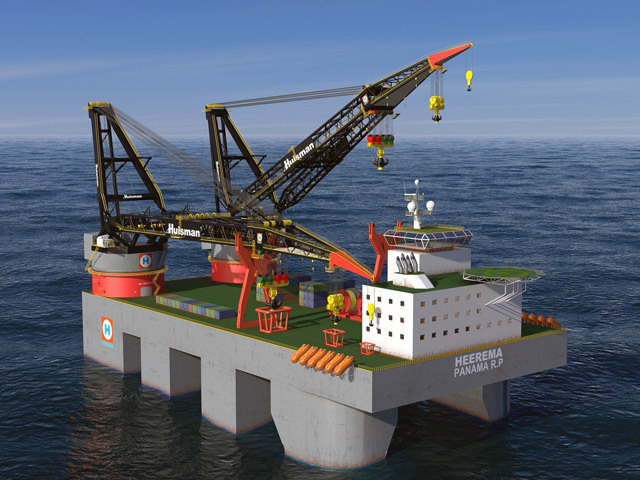
Dutch heavy lifting specialist Heerema Marine Contractors is preparing to set a new record by ordering the largest construction semi-submersible ever.
It will have a designed maximum tandem lifting capacity of 20,000 tonnes and it is fellow Dutch company Huisman that will design and build the two enormous 10,000 tonnes capacity cranes required.
The new vessel’s capacity marks a big advance on current heavy-lifters. These comprise Thialf with a twin crane (tandem) lift of 14,200t, Saipem 7000 (14,000t tandem), Svanen (8.700t), Hermod (8,100t tandem), Lan Jing (7,500t) and Balder (6,950t tandem).
HMC has already signed an agreement with engineering company GVA to develop the basic design package of the new crane vessel.
The NSCV will have a length of 214m and a width of 97.5m, making it the largest crane vessel in the world.
The vessel will have a designed transit speed capability of 10 knots.
HMC says that, during the design a lot of attention is given to ensure the vessel meets the highest health and safety standards and reduce the environmental impact during fabrication and operation to a minimum.
It is not known where this behemoth will be built, but the assumption is that it will be in the Far East. A final decision on the project is apparently to be made before the end of this year.
Turning to the letter of intent between HMC and Huisman, each crane must be capable of lifting 10,000 tonnes in revolving mode.
The jib of each unit will have a length of 145m. With the jibs (booms) up, the heavy-lifter will have an air-draft of 210m.
Operating radius will be 48m. The cranes further feature a 2,500-tonne auxiliary hoist and a whip hoist with a maximum reach of 155m.
HMC’s CEO Jan-Pieter Klaver said in a very brief statement: “The LOI with Huisman is as an important step on the critical path for Heerema Marine Contractors to introduce the NSCV to the market”.
Huisman is to build the cranes at its production facility in China.
Unlike traditional “tub” cranes which make use of either bogies or large wheels for their slew system, the Huisman cranes will utilise large bearings of its own design which are manufactured in-house.
This technique apparently represents a step change in the crane industry, and was previously used successfully on the 5,000-tonne offshore mast crane installed aboard Subsea 7’s Seven Borealis and the 4,000-tonne OMC for HMC’s Aegir, which was delivered late last year.
According to Huisman, the use of bearings on the new 10,000-tonne cranes instead of the traditional slew systems allows for very accurate control of the slewing motion of the crane and requires very little maintenance.
Another major benefit of using a bearing is a very significant weight saving. This is an important feature, especially on semi-submersibles. The slew bearings of these huge cranes will have a diameter of 30m.
Recommended for you
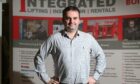