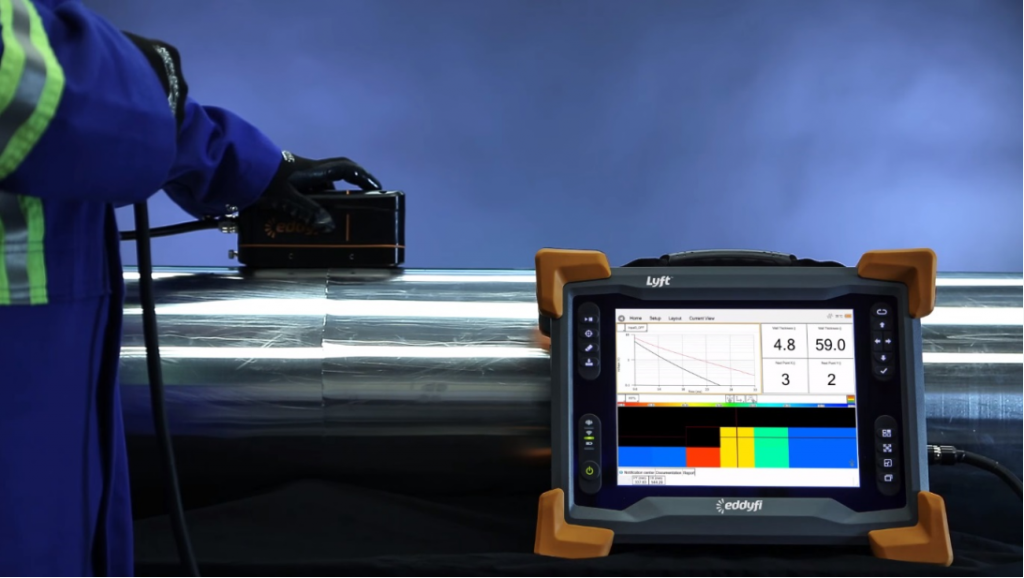
Bilfinger Salamis UK can reduce labour costs and provide optimum results
Corrosion under Insulation (CUI) is perhaps one of the most significant integrity threats that the oil & gas industry faces today.
Water ingress causes damage to pipework and other susceptible steel elements, but the corrosion process underneath existing insulation materials is one of the most difficult to prevent.
CUI can also be a difficult problem to detect, as Sandy Bonner, chief operating officer at Bilfinger Salamis, explains: “By the time insulation is removed and corrosion detected significant damage may have already been done.
“The most common inspection technique used for CUI is to simply remove the insulation and perform a visual inspection initially. The removal and reinstatement of insulation is a significant logistical exercise which in some cases requires restricted operation.
“It is labour intensive, expensive and in many instances completely unnecessary as the substrate can often be found to be in good condition. We believe it’s time this changed.
“With that in mind, Bilfinger Salamis has invested in solutions that allow asset owners to monitor the condition of insulated pipework more efficiently.”
End-to-end efficiency
Thanks to its highly-skilled rapid close visual inspection (RCVI) teams, the company manages CUI issues through a single point process – one contact and one contract. RCVI teams consist of multi-disciplined rope access personnel who can quickly deploy a range of CUI management processes.
These teams include specialists for access, survey inspection, and advanced NDT, as well as coatings, insulation and other specialist areas.
The RCVI teams can quickly access remote areas, conduct an initial survey to highlight potentially sensitive areas, perform relevant inspections, conduct any coating repairs, reinstall insulation and have an asset back in working order with minimal interruption to service.
Archie Crawford, technical authority – non destructive testing at Bilfinger Salamis, said: “Our focus is on minimising resources needed to carry out the work. To this end, our inspection and fabric maintenance departments work together, using small three-man multi-skilled teams that include an inspector, insulator and painter, all of whom are rope access qualified.”
Bilfinger are in a unique position within the industry to be able to combine all of the above services into one multi-disciplined team, reducing labour costs and providing optimum results for asset owners.
Advanced detection technology
Together with speeding up site inspection processes, ensuring teams are equipped with the latest advanced CUI detection tools, such as digital radiography and pulsed eddy current (PEC) technology, is key.
Bilfinger owns and uses handheld Eddyfi PEC systems for rapid real-time inspection data of wall thickness with full traceability.
In addition, the business is investing in technologies aimed at reducing the time required for inspections including unmanned aerial vehicles (UAVs).
Crawford said: “There is now a lot more that can be done to detect hidden corrosion than simply carrying out visual detection. Using advanced imaging techniques that make use of non-visible electromagnetic effects to detect the condition of pipework means we can get a much earlier and more reliable indication of issues.
“While both radiographic and PEC imaging have been known about for a long time, the technology used to carry out inspections has advanced rapidly in recent years.
“Where each radiographic exposure once took several minutes to capture and subsequently needed to be processed using lab equipment, we can now carry this out in a matter of seconds and have images to view there and then on a mobile device.
“Similarly, where PEC readings as recently as five years ago needed to be carried out on a point-to-point basis, making it time consuming to capture all of the angles and positions required to scan a length of pipework, the latest Eddyfi systems run continuously. This cuts the time required and significantly increases the number of data points available, providing greater certainty of results.”
Sandy Bonner concluded: “Offering our clients the latest technology for managing and monitoring CUI is critical, especially where ageing infrastructure is involved.
“Combining knowledge and capability across a range of disciplines makes the management of CUI a seamless process, helping asset owners manage the threat of CUI in the most effective and efficient way possible. ”
Bilfinger Salamis UK is exhibiting its CUI technology at the Energy Institute’s Asset 2016 event at the Marcliffe Hotel, on Tuesday, October 4