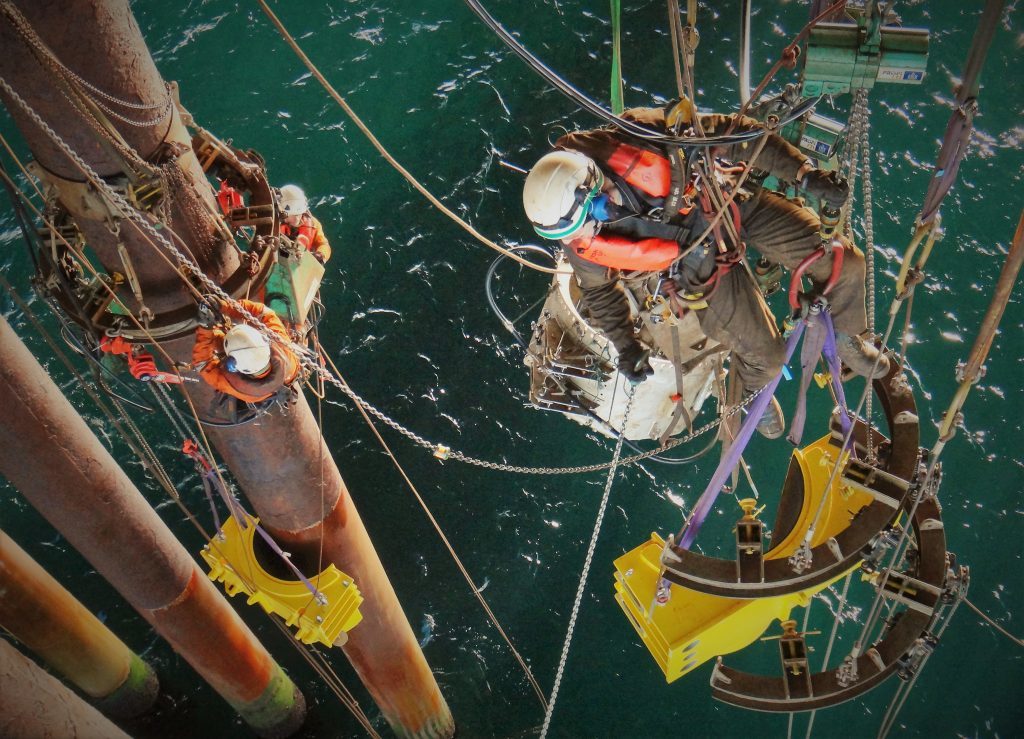
It was a highly unusual collaboration between two companies based in Aberdeen that had not previously worked together. They are SETS and TRAC.
It delivered cost savings to a Northern North Sea operator client that many in the offshore industry dream of but can’t get anywhere near.
The bill was £2.5million compared to £8.4-27.3million, had diver-based solutions been conventionally applied.
And its marriage of rope access techniques with subsea remote intervention fits perfectly the kind of imaginative solutions that are required to enable ageing production assets to remain viable in an energy province renowned for high costs.
“This is really about collaboration and how effective it can be,” said SETS MD Chris Tierney.
“A lot of the industry’s been discussing collaboration over the last two years but the reality is that it’s not really been happening.
“Contractors are the ones who seem to be driving this; not the operators and others who stand to benefit the most.
“Some of it happens by accident and that applies to us too. SETS was approached by a client (operator) to look at what had historically been a subsea problem and come up with a different way of carrying out inspection, cleaning and repairs.”
In essence, this task was about eliminating the most expensive piece of hardware from the equation . . . a dive/ROV support vessel.
What if the work could be done directly off the platform without interrupting production and routine well intervention operations?
SETS has a lot of intervention experience within its team, including from the operator’s side and the cost reduction drivers that go with.
Tierney: “Replacing the vessel became quite easy because the work we had been asked to do was close by the platform; the challenge was to come up with a method of delivering the solution by working with TRAC.”
Jan Stander, business delivery manager at TRAC, said: “Working together, we looked at different aspects of tooling; SETS went out to the market to look at technologies that existed and set out to change that.
“Then we developed and tested both the tooling needed and the way of delivering that tooling down to the worksite. It became a natural progression and was very successful.”
“Initially, taking existing technologies and deploying them using rope access techniques proved to be a bit more of a stretch than we anticipated.
“So new tools were developed to enable the deployment of remote cleaning, inspection and applying repairs required.”
That tooling included developing a split clamping device call the “donut”, a lifting aid that gave a repeatable means of deploying equipment in exactly the same way on every location.
This cut down the amount of upfront engineering time that might otherwise have been needed.
Stander said: “Two teams of four rope access technicians plus supervisors carried out the work on the platform’s conductors.
“A cleaning team would start off; once they were done the second team came in behind to carry out the repairs. TRAC’s total headcount offshore was just 11.”
The actual work location on the conductors was at minus 12m and the tooling was deployed from a location 16m above the splash zone.
Once the equipment was delivered to site subsea, tooling cameras helped to confirm positioning, supporting the rope access team suspended above the work location.
A subsea laser to take metrology readings between various components was used to inform as to which type of repair should be deployed if required.
The team mobilised early August and completed mid-October.
The client thought that eight conductors needed looking at and possibly repaired but things turned out a little different.
Stander said: “It was taking one day for cleaning and inspection and giving the client results once we were actually on site. Then it was one day for installing one type of clamp and two days to instal another type of clamp. Within four days we were rigged up, inspected and derigged from the actual conductor itself.
“We inspected a total of 14 and installed repairs to seven of them.
“This sort of work is important to any operator planning the late life of an asset, including whether it is worthwhile carrying out actual repairs to conductors.”
What’s the future for this collaboration?
“We’re concentrating on making other operators aware that the approach used by SETS with TRAC works well,” said Tierney.
“We’re already discussing other types of workscope where we can work this way.
“We have the team; it’s a matter of looking to see what else we can do using TRAC essentially as our vessel and the engineering team delivering IRM/Opex solutions below the waterline.”
Stander and Tierney are clear; there’s a growing interest in what SETS with TRAC achieved.
The people who control the budgets within operators are more willing to listen than in the past.
Traditionally the budget for this sort of thing would simply go to subsea and they would go and hire the DSVs. Not any more, it seems.
Recommended for you
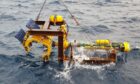