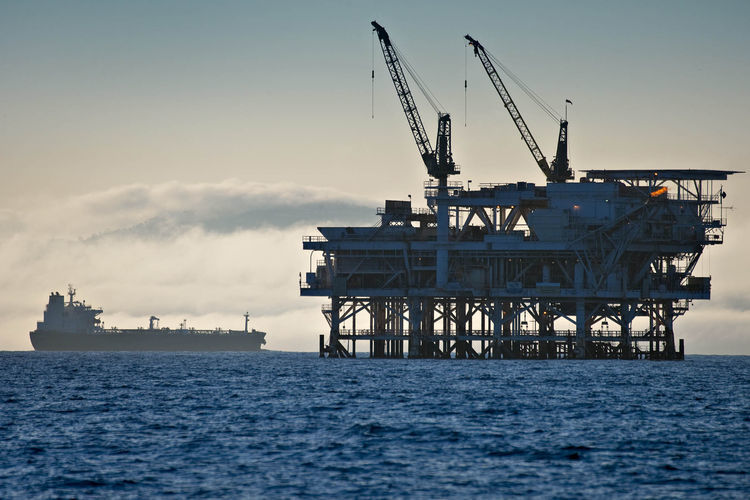
In this, the first of a series of bi-monthly articles, I’m taking a general look at how financial decision-making during new offshore construction may have long-term consequences due to degradation mechanisms.
Managers, engineers, plant inspectors and fabric maintenance contractors engaged in the management of asset integrity have an affinity toward one precious metal – ‘ferrous steel’.
There are others, of course, but ferrous steel remains king amongst the materials of economic choice in the oil & gas industry.
Steels are alloys based on iron (Fe) and have been around for millennia.
They are ubiquitous in their use, not least pipework, vessels, valves and of course the very ships and most of the platforms that populate the offshore oil & gas industry.
Problem is that it rusts and now the gauntlet has been thrown down to asset owners to ask themselves: “Corrosion erodes your safety margins and bottom line – do you want to risk it?”
A little tongue-in-cheek perhaps but there’s industry recognition that, as we extend an asset design life to capture the remnants of hydrocarbon, we entertain ageing consequences and risk assess to minimise threats accordingly.
But what if the very foundations of our mathematical algorithm assumptions do not hold water, if you’ll pardon the pun?
The industry has developed mechanical and composite intervention methodologies that are engineering genius. These technologies exceed original design intent and have a lifecycle equal to or better than required for the whole of production life – and it’s not just in the oil and gas industry that these technologies have an established market share.
When a decision is made to cut investment during a new construction build, the real challenge lies in the distant future and in a predicted deterioration scenario that can be forecast based on the knowledge amassed by agile and predictive database tools.
The operating company vision statement should be the construction project strapline, otherwise the spectre of corrosion will be lost in the euphoria of budget cut success.
Reflect as you go about your daily business: new fixed, floating or mobile asset design lives require appropriate investment and material specifications with a Whole of Life approach that ensures a maintenance programme of prevention rather than intervention.
It’s more cost-effective to schedule remedial corrosion protection, however done, and prioritise it with the support of key management stakeholders.
Taking a pragmatic view on what would be an optimal coating and thermal insulation specification of a new-build for long-term maintenance-free operations takes a little bit more thought but it’s good news.
Such systems are available with excellent track records, they’re cost-efficient and effective to meet project demands at the outset.
MCL Protection Ltd is a specialist provider of corrosion, coatings and asset integrity solutions to the energy industry.
Operating globally, the company has extensive heavy fabrication yard and offshore project management experience and a proven track record in problem-solving for the emerging integrity needs of the asset owner.
Recommended for you
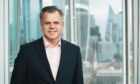