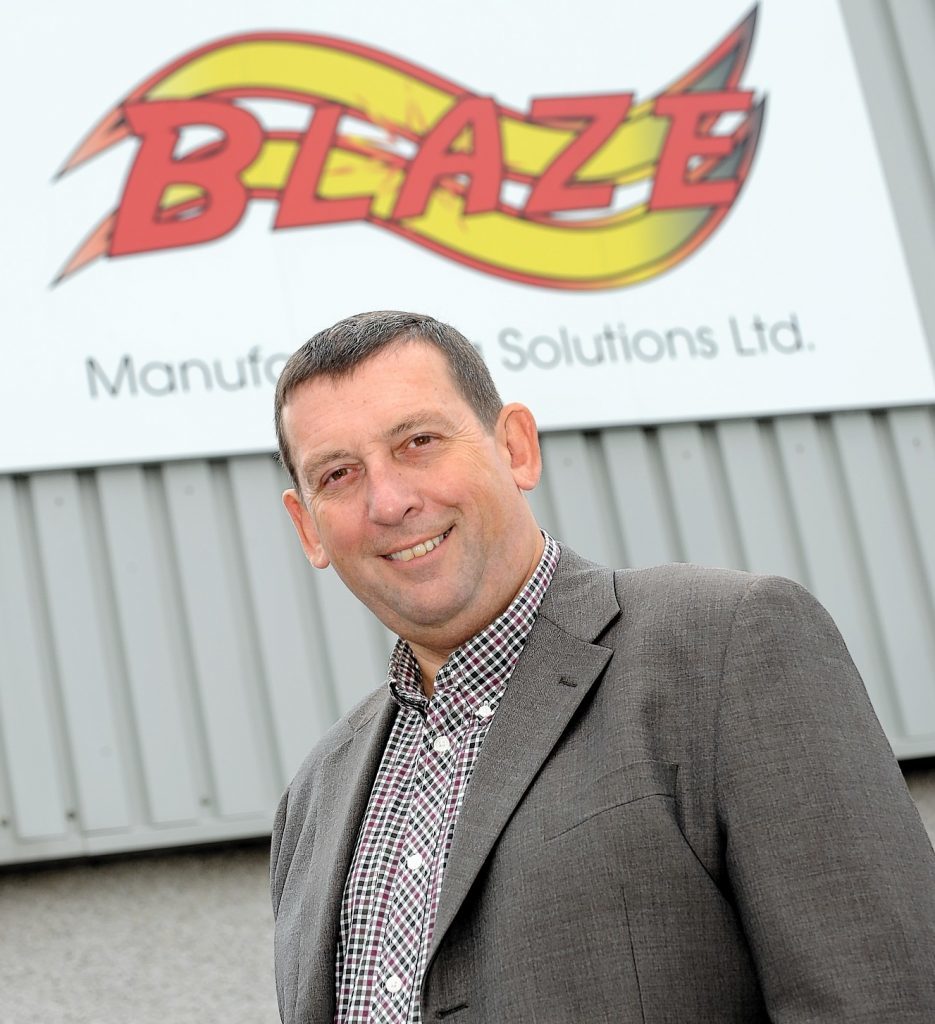
2018 has so far brought an increase in activity across the oil and gas markets. Brent crude is trading at a three-year high, with more rig movements and drilling activity as a result. This is looking very positive and our focus for 2018 is to reduce the environmental impact of regular testing and maintenance activities on assets.
Blaze systems range from gas suppression, firefighting foam and firewater deluge systems and we have been developing them to have a lower carbon footprint. For gas suppression, we avoid discharging systems by undertaking integrity testing to ensure that fire extinguishing concentrations will be held for the required time, negating the requirement to discharge the suppression agents into the atmosphere. Carbon dioxide levels are higher than ever, a contributing factor to the extreme weather events we see all over the world. Blaze no longer use agents that have longer atmospheric lifetimes – in some cases, 1kg of gas could be in the atmosphere for 300 years.
In 2015, the US Environmental Protection Agency founded the PFOA stewardship programme for firefighting foam manufacturers worldwide to commit to the withdrawal of products containing fluorosurfactants having a carbon chain length greater than C6.
This change has a significant impact on firefighting foam users. Biodegradable synthetic-based fluorine-free products are now widely used. However, foam agents that do not contain fluorinated surfactants usually contain higher concentrations of hydrocarbon surfactants and solvents to compensate for the lack of film formation. This results in a more acute aquatic toxicity than the agents they replaced.
There are alternatives to discharging firefighting foam and when testing of foam producing equipment is required, we recommend the use of test foams that do not have detrimental environmental impact.
On the firewater deluge side, problems can arise with nozzle blockages from either marine or corrosion verdigris. To prevent this, Blaze has developed a filter that can be retro-fitted into most nozzles which will be provided free of charge as part of any testing or maintenance programme.
Wet-testing cannot be completely eliminated, but the impact versus the benefit must be fully considered. Dousing the topsides plant with seawater is not desirable as this exasperates corrosion and plant failure. In response, we have developed complementary test regimes ranging from smoke testing, dry testing of equipment, borescope inspection and wall thickness verification. This is offered as part of a maintenance programme which reduces the need to undertake frequent wet-testing.
Many fire protection systems and performance standards contain requirements for periodic inspection, testing and maintenance (ITM). These are generally based upon historical requirements and not on any field data or on observed deficiencies.
The National Fire Protection Association (NFPA) has developed new documents, such as NFPA 4 on Integrated Testing of Fire Protection Systems, recognising the need for a more data-based approach to ITM frequencies.
Accepted by verification bodies, Blaze uses this approach for delivering and optimising inspection, testing and maintenance routines, reducing the impact on plant and sub-systems.
Let’s make 2018 the year where we clean up our act!
Howard Johnson, managing director, Blaze Manufacturing Solutions