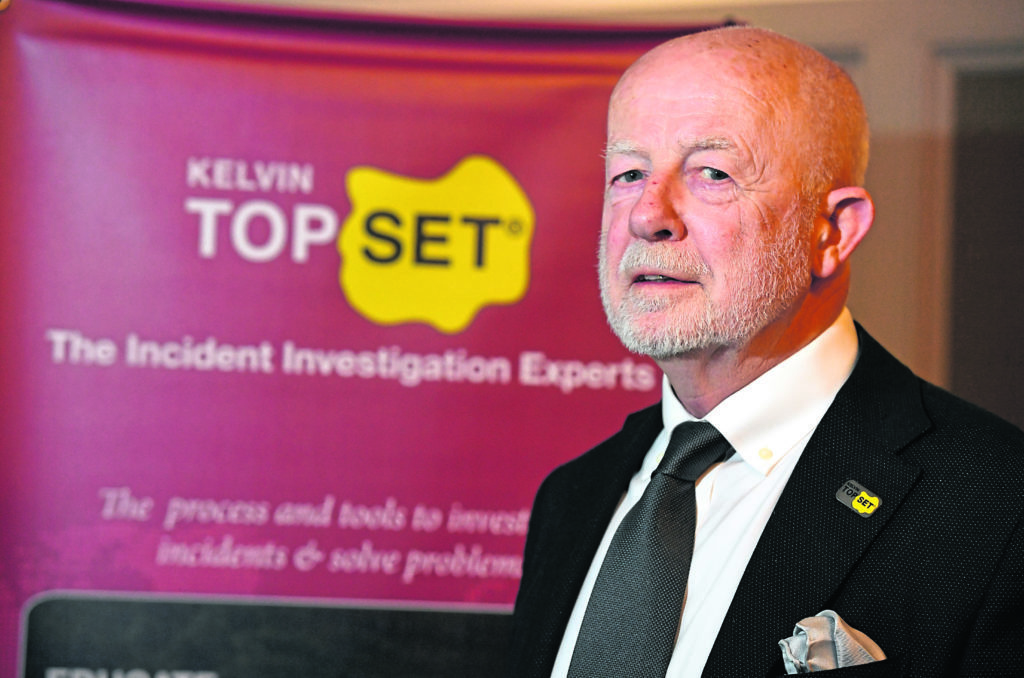
Human factors are at the heart of all major offshore incidents, indeed all incidents, an investigation expert has recently stated. David Ramsay, group managing director of industry specialists Kelvin TOP-SET, made the comments as he was reflecting on the 30th anniversary of the Piper Alpha disaster.
He said that while technical faults do occur, ultimately these arise from a combination of errors which can usually be attributed to failures in communication.
“It has been 30 years since Piper Alpha”, he said. “Sadly, incidents still occur, but as we all know, Piper was a game changer. Since then, companies have invested heavily in seeking to prevent similar tragedies. This is one of the reasons businesses such as mine, helping to prevent incidents occurring, were established.
“It was widely recognised that things had to change. As a result of this, there has been very significant investment in establishing the causes of error, and many techniques and systems have been established to identify how changes and improvements can be made. However, in the 30 years since Piper, I have led many investigations, and I can say that, at the heart of every one, there has been a communication problem.
“I was involved heavily in the Deep Water Horizon investigation. On the day that rig blew up, it was actually being given an award by BP for incident-free operation. Decent people trying to do a good and safe job, but there were hidden failures at the heart of the system. People don’t do daft things deliberately, they want to go home at night or at the end of their tour offshore, and yet, tragically, 11 men died and all others had their lives changed.”
He said one of the biggest problems occurring is that there are usually small indicators, or “weak signals” that may not seem significant at the time, but may have huge escalation factors creating a potentially high-risk situation. When incidents do happen, these apparently minor failures all come together. There is never just one single cause.
He added: “We need to understand why these factors are missed, and yet subsequently combine to create possible disasters. It is never just as simple as someone making a mistake – it is the situation in which they and others have been placed.
“Quite often, companies are keen to blame what has gone wrong on technical failures, but it must always come back to human factors and communications. Think about it – machines, processes and systems are the result of human thought and human action.
“A big part of what we are doing is trying to identify communication failures.
“I’d like to quote Steve Rae, a Piper Alpha survivor who, at the recent conference here in Aberdeen, said: ‘Training in non-technical skills, such as communication and leadership, must be improved. We owe it to these individuals to start investing in the competence of soft skills.’”
Mr Ramsay, whose company, Kelvin TOP-SET, has been working in the oil industry since 1986, said he also believed his company’s investigation and problem-solving model helps companies look at themselves.
“We stand out because we are able to quickly and effectively establish the contributing facts and root causes,” he said. “Even when companies have carried out their own investigations, they often tell us that we have been much more comprehensive, have gone much farther back in time and yet produced our results and conclusions quickly.
We help them see that helping people to communicate more effectively does result in safer operations.”
Improvements after investigation course
Aidyngali Tyshkanbayev, field production superintendant, Maersk Oil/Total, who introduced TOP-SET to Maersk in Kazakhstan when he was head of HSE, said: “Since members of our management team attended their TOP-SET lead investigators and special incident investigation course, our company has enhanced its way of managing incident investigation. We have noticed significant improvement in the quality of our investigations, in getting down to the root causes, and in developing preventive actions to tackle identified root causes.”
In the best position to probe incidents
Diamond Offshore is a leader in offshore drilling, providing contract drilling services to the energy industry around the globe with a fleet of 17 rigs, consisting of 13 semisubmersibles and four dynamically positioned drillships.
Dirk McBain, HSE supervisor, said: “2013 saw a game changer in the way we investigate incidents. Every HSE manager and supervisor now attends the three-day TOP-SET senior investigator course. This has enhanced our problem solving skills.”
Kelvin TOP-SET is the first choice
Kenneth McKechnie, QHSE Culture Lead with Mitie Group PLC, said: “I’ve been a forensic crash investigator for the police in both the UK and the US for more than 21 years. My first use of the Kelvin TOP-SET methodology was in an HSE culturally “well developed” oil firm, where it provided us with a reliable standard language for investigations.
“I’ve moved to a new challenge in the facilities management sector and Kelvin TOP-SET is the problem solving and investigation methodology we have chosen.”
Recommended for you
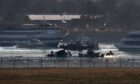