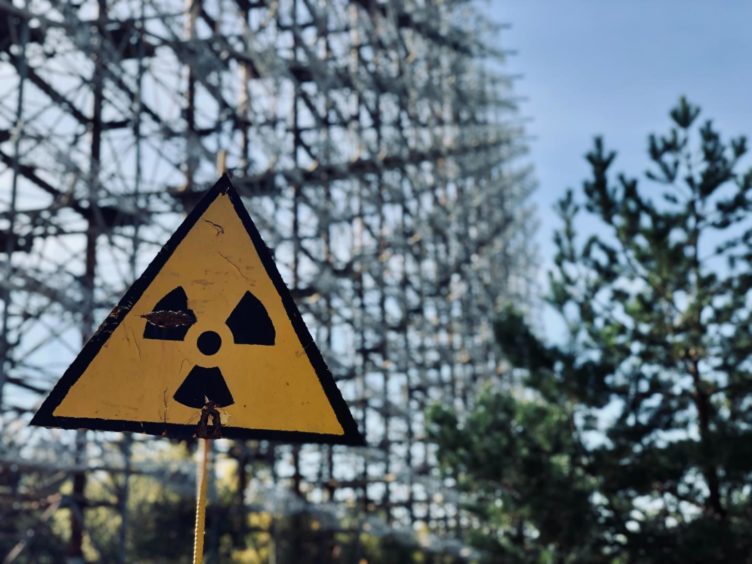
Every year, in all industries, millions of workers suffer from ill health caused or made worse by work. And I’m not just talking about injuries or accidents that are reportable to HSE, but health problems alongside aches and pains that are directly related to your occupation and work environment.
Of course, regulations and standards are in place to help prevent this from occurring, with more HSE professionals finding an increased importance being put on their role in order to improve work environments.
But what we must be aware of is that workplace dangers are not always as obvious as a falling piece of equipment or trip hazard. With that in mind, close attention should be paid to certain areas and tasks that may put a worker’s health in jeopardy.
International SOS can advise its clients on such dangers as part of its industrial hygiene service. This service offers insight into the science behind mitigating the risk of industrial and manufacturing hazards from harming workers.
Using evidence-based scientific procedures, industrial hygienists measure toxic agents such as dust, fumes and noise in the work environment to then accurately advise organisations on how to manage these risks to a practicable minimum, while achieving legal compliance.
Four tips for improving your employee safety through industrial hygiene are:
1. Understand the risk
A risk assessment should be carried out to understand the different hazards present in the workplace. The analysis comprises three main stages: identification, analysis and then establishing an acceptable risk level. The process should be repeated, periodically re-testing risk levels to make sure effective controls are in place, and all new hazards accounted for.
2. Form exposure groups
Similar exposure groups (SEGs) look at similar general hazard exposure among groups of different people. They’re formed by comparing job roles, processes, locations, demographics and other relevant factors. When forming SEGs, consideration should be paid to unplanned and infrequent events, diversity of tasks among your workforce and collaboration of work and projects, which may expose employees to further hazards.
3. Track and maintain your assets
ISO standards require you to record assets and adopt measurement and calibration systems to control the production and maintenance of products and equipment. Not only is this a requirement, it’s also an important step in improving employee safety. Automating these processes lets you stay on top of your equipment for improved safety.
4. Keep employees informed
Training employees on all industrial hygiene practices keeps them knowledgeable and accountable, increasing safety. We’d recommend integrating industrial hygiene processes with all other aspects of your employee safety plan.
Getting your industrial hygiene processes in check can effectively improve workforce safety, which will, in turn, lead to a more productive work environment.
International SOS can supply industrial hygiene services globally and can both manage and provide governance to these services. For anyone interested in finding out more please contact Claire Westbrook-Keir, International SOS director of key account management: claire.westbrook@internationalsos.com