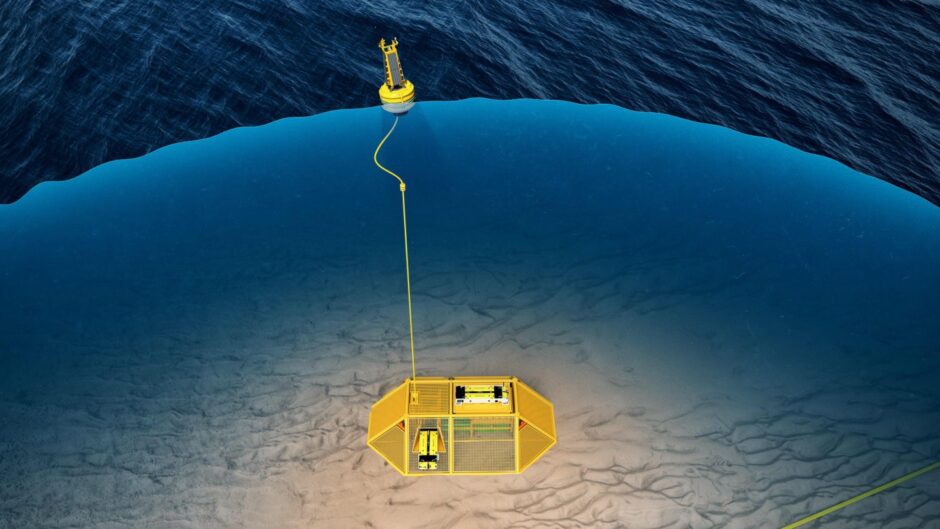
Over the next ten years, the Global Wind Energy Council predicts that more than 380GW of offshore wind capacity will be added across 32 markets.
Asia-Pacific will account for nearly half of this growth, with 41% in Europe, 9% in North America and a further 1% coming from Latin America.
Early in the development process of offshore wind farm foundation sites, a range of surveys are conducted including geophysical, cable route and unexploded ordnance.
This is generally before final investment decision, so survey cost reduction and improved accuracy can contribute to reduced development risks.
Geophysical seabed survey tasks are typically performed using large-scale arrays towed behind diesel-powered survey vessels and some verification using tethered remotely operated vehicles.
These vessels tend to be older, repurposed vessels with high carbon emissions and are subject to curtailed weather working windows outside of the summer months.
The offshore wind industry therefore needs a new approach to pre-development surveys in order to reach the targets of new wind farm roll-out, as well as aligning surveys with net-zero targets.
Verlume, with its extensive track record in subsea engineering and energy storage systems, has developed an offshore charging system which allows autonomous underwater vehicles (AUVs) to dock, recharge batteries multiple times, upload survey data and receive new mission data without requiring extensive intervention.
The system, named Airies, is placed on the seabed within the field of operations and integrates four building blocks of existing technology: a seabed energy storage power and communication gateway, a communications buoy, multiple AUV docks and a software interface.
Industry standard sub-bottom profiling equipment is used in conjunction with the AUVs. The ability to perform 3D surveys is also being considered, where a sub-seabed 3D model is created, reducing repeated surveys over the same site.
The system is designed to recharge AUVs multiple times before the battery units are recovered to the vessel deck, charged while the vessel is relocating and then re-submerged to another site. Alternatively, batteries can be powered in-situ using renewable energy or charged via surface vessel using a downline charging cable.
By utilising this new approach, there is less reliance on carbon-intensive traditional vessels which are often in short supply.
The resident underwater vehicles are also less susceptible to adverse surface weather conditions than the typical vessels used.
Costs are reduced through less reliance on launch vessels and personnel to support this. Another major benefit is that safety and reliability of operations is improved by removing safety implications associated with sending personnel offshore.
The Airies system can be placed infield as a resident system for standard visual inspections.
This is particularly useful within floating offshore wind where requirements for regular inspection of dynamic cables, moorings, anchors and subsea buoyancy systems are critical.
The full Verlume system will be trialled later in the year to demonstrate a new approach to seabed surveys and inspections as part of the global push to increase offshore wind farm capacity.
Recommended for you
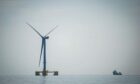