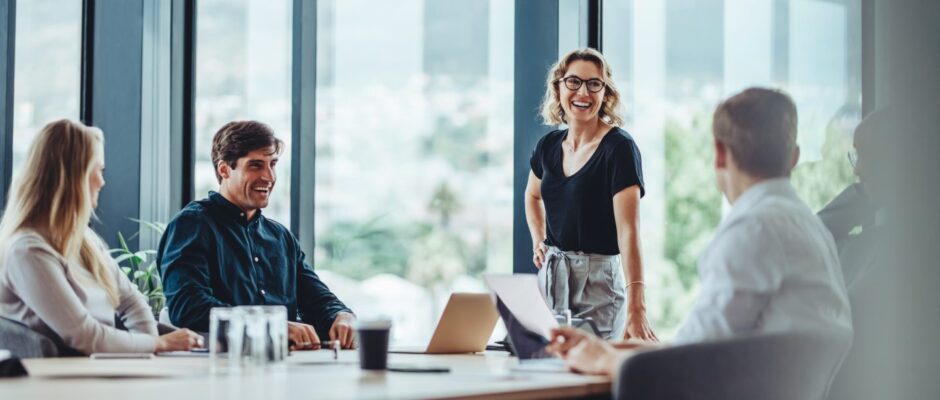
Bilfinger UK’s continuous improvement manager and head of digitalisation and innovation, shine a light on Operational Excellence and what it involves.
Maureen Leiper, continuous improvement manager, and Mark Kelly, head of digitalisation and innovation, both from Bilfinger Engineering and Maintenance UK, delve into what is Operational Excellence (OPX) and how it brings together continuous improvement, digitalisation, innovation and standardisation.
In today’s dynamic business landscape, organisations face relentless challenges to stay competitive, efficient, and sustainable. For Bilfinger UK, embracing Operational Excellence (OPX) through continuous improvement and digitalisation isn’t just a choice—it’s a strategic imperative.
Maureen Leiper, continuous improvement manager at Bilfinger Engineering and Maintenance UK, explains: “At its core, continuous improvement is about incremental progress—a commitment to refining processes, enhancing performance, and driving positive change. It’s not a one-time initiative; it’s a mind-set that permeates every aspect of an organisation. Companies that thrive understand the necessity of not just adapting to change but embracing it proactively.
“In the case of Bilfinger UK, this philosophy manifests itself in the relentless pursuit of continuous improvement across all facets of our operations. Sometimes those improvements are big, often they are small. But what’s most important is that they are frequent.
“We understand that the most valuable asset within any organisation is its people. That’s why we invest in the development and empowerment of our employees, providing them with the tools, resources, and opportunities to innovate and excel in their roles.”
‘Lean thinking’ to achieve sustainable change
Bilfinger has invested heavily in training the Lean 6S methodology available to executives, managers and employees working in both operations and administration.
The methodology provides ‘lean thinking’ in order to achieve a sustainable change in operational performance. Rolling out Lean management training is key to building and developing Bilfinger-wide Lean know-how so it can continue on the journey to becoming number one in efficiency and sustainability for customers.
Speaking of the value of the Lean training, Maureen added: “I got the opportunity to join Lean Expert training Wave 2 in 2022 along with eight colleagues from across the Bilfinger Group. This involved attending intense training weeks in Oberhausen, Neu-Isenburg and Stenungsund. In parallel, I led my Lean project team to solve a problem relating to ongoing IT license costs following the leaver’s process.
“I have since joined the LEAN@Bilfinger programme as a trainer, where I share the knowledge and skills I learned with others. Coaching Bilfinger UK trainees through their lean projects is particularly rewarding.”
Mark Kelly, Head of Digitalisation and Innovation at Bilfinger Engineering and Maintenance UK, adds that OPX brings together continuous improvement, digitalisation, innovation and standardisation to achieve this journey.
He said: “OPX allows us to leverage the opportunities provided through continuous improvement and apply digital technologies and innovative practices within the same workflow to create standard, scalable solutions. Applying this thinking ensures that not only do we provide the efficiencies and improvements, but we also enhance our operations and deliver value-added solutions for the future across our services.
“Digitalisation can be perceived as a heavily technology-based approach but although technology is a key part of it, achieving true digitalisation or digital transformation has to focus on using digital technologies to transform business processes, products, and services as part of a wider improvement drive. Digitalisation can be used to improve efficiency, quality, customer satisfaction, and in some instances revolutionise ways of working, but this must be done in a way that delivers for the business and services, OPX is our way of ensuring this.”
“Standing still in a rapidly evolving world is akin to moving backward”
Mark continues: “By integrating digitalisation into OPX, we use it to enhance optimised processes and operational practices, defining more standardised ways of working and solutions that can be easily transferred across our contracts. We lever these technologies and platforms to upskill our teams and accelerate the adoption and drive for digitalisation throughout our operations.
“Standing still in a rapidly evolving world is akin to moving backward. Therefore, we have made it our mission to continuously evaluate, innovate, and enhance our processes, systems, and services to stay ahead of the curve. Technology is obviously key when we think of innovation but alongside the work we are doing in robotics, automation, AI and asset management we have a keen focus on more operational innovation.
“These projects can start in any area of OPX as a localised continuous improvement project, application of digital tool to change the way a process operates, or just application of best practice. We believe that innovation can happen in any part of our business at any time and OPX is here to support that.”
Mark concluded: “OPX streamlines operations, reduces waste, and creates value. For Bilfinger UK, this translates to smoother project execution, shorter turnaround times, and cost savings to Bilfinger and our clients.”
Recommended for you
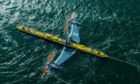