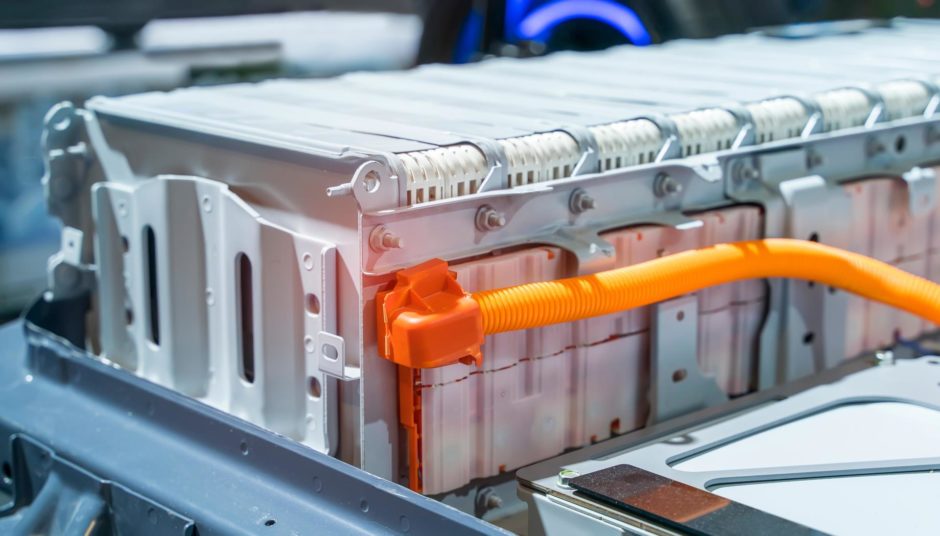
With the greatest and most urgent energy transition in human history clearly accelerating, the quest for new technology solutions across multiple and increasingly diverse low carbon fronts is becoming ever more important.
There’s a lot of “blue sky” work of the kind most readily associated with universities and government institutions going on.
They are heavily involved in finding new ways of making what we already have a lot more efficient.
Because of their huge importance to our cleaner, greener future, much of the research and development of future power generation and energy storage technologies is concentrated in universities.
Because of its strategic importance, the work attracts a significant amount of corporate and public purse funding, especially within the EU, Asia-Pacific, particularly China, and the US.
Photovoltaics, where massive efficiency gains have been achieved over the past decade, and batteries, where progress has been less spectacular, are excellent examples of sponsored, targeted R&D funding.
And it is the humble battery that part one of our two-part tour of research labs around the globe is focused on. Read our February edition for the second instalment.
With the exception of fossil fuels, it’s the only large-scale means of storing energy that humankind has so far come up with other than reservoirs and rivers linked to hydropower.
Batteries are fundamental to green energy storage and widely recognised as a fundamental enabler of the transition.
But they need to be a lot more efficient than the current mainstays — lead-acid and lithium-ion (Li-ion).
The former powered the first electric vehicles more than 100 years ago and is still a workhorse today, especially for starting up internal combustion engines and providing emergency lighting.
The first commercial Li-ion batteries were developed by Sony in the early 1990s and have become the battery of choice for the electric vehicle revolution.
Around 17,000 EV cars were on the world’s roads in 2010. By 2019, that number had swelled to 7.2 million and Deloitte is forecasting over 30 million by 2030. That’s not counting the growing population of EV buses, delivery vehicles and other forms of public transportation.
Battery storage for stationary applications looks set to rocket from only two gigawatts (GW) worldwide in 2017 to around 175 GW. It is already popularly linked with home PV installations and wind turbines.
But batteries are a long way short of being as efficient as their potential suggests.
We are spoilt for choice when it comes to providing a taste of university-based research projects regarded as important to the quest for a better battery.
We have selected four. Two are Li-ion focused and two relate to a totally new generation of battery that could displace lithium as the long-term element top choice.
Latest lithium fixes
While EVs hold promise for a more energy-efficient, less polluting personal transportation future, among their limitations is the lack of a long-lasting, high energy density battery that increases their range without the need for recharging.
By the same token, for homes during blackouts, small, efficient emergency batteries able to power domestic needs for more than one night without don’t exist.
Academics and industry are hungry for a new generation Li-ion cell that genuinely offers high-energy capacity, lightweight, long-lived, safe and low-cost energy storage.
But there are a number of major obstacles to overcome and one of them is how best to protect the lithium metal battery anodes from operational damage.
While rechargeable anodes play a key role in how well this new wave of lithium batteries function, they are highly susceptible to the growth of dendrites – microstructures that can lead to dangerous short-circuiting, potentially catching fire and even exploding.
Researchers at Columbia Engineering, an offshoot of the Ivy League research institution Columbia University, have discovered that alkali metal additives can prevent this dendrite proliferation during battery use.
They have utilised and applied a combination of microscopy, nuclear magnetic resonance (similar to an MRI), and computational modelling to discover that adding small amounts of potassium salt to a conventional lithium battery electrolyte produces unique chemistry at the lithium/electrolyte interface.
Potassium ions mitigate the formation of undesirable chemical compounds that deposit on the surface of lithium metal and prevent lithium ion transport during battery charging and discharging.
Commercial electrolytes are a cocktail of carefully selected molecules. By using nuclear magnetic resonance and computer simulations, the Columbia team has been able to understand how these unique electrolyte formulations improve lithium metal battery performance.
This insight ultimately gives researchers the tools they need to optimise electrolyte design and enable stable lithium metal batteries.
Safety issues are occupying a research team at Tokyo University, whose members have come up with a way to not just improve safety, but enhance performance too by providing more charge.
“A battery’s voltage is limited by its electrolyte material. The electrolyte solvent in lithium-ion batteries is the same now as it was when the batteries were commercialised in the early 1990s,” Professor Atsuo Yamada said.
“We thought there was room for improvement, and we found it. Our new fluorinated cyclic phosphate solvent electrolyte greatly improves upon existing ethylene carbonate (EC), which is widely used in batteries today.”
EC is notoriously flammable whereas the phosphate solvent electrolyte isn’t. The extra bonus is that it can also cope with higher voltages.
As lithium ion-powered EVs proliferate, this additional safety and power punch will doubtless be well received by the market when commercial production eventually starts.
Graphite is a fundamental part of the typical Li-ion cell as it is used as the anode. But it has limitations that scientists at the US Department of Energy’s Pacific Northwest National Laboratory (PNNL) appear to have found the means to overcome.
They have devised a way to make a single-crystal, nickel-rich cathode that is both tougher and more efficient.
Nickel has secured the attention of various lithium-ion battery makers, largely because of its relatively low cost, wide availability and low toxicity compared to other key battery materials, such as cobalt.
Nickel-rich cathode materials have real potential to store more energy but large-scale deployment has been a “challenge”, according to Jie Xiao, PNNL project team lead.
First off, there is a fine balance to be achieved as, in large amounts, Nickel can pose problems by making cathodes less stable. High nickel content can increase unwanted side reactions, damaging the material and making storage and handling very difficult.
The most common nickel-rich cathode comes in the form of polycrystals – aggregates of many nanocrystals in one larger particle. These carry advantages for storing and discharging energy faster.
Polycrystals sometimes break down, leaving the surface area exposed to the electrolyte, accelerating unwanted chemical reactions induced by high nickel content and generating gas.
This irreversible damage results in a battery with a nickel-rich cathode that fails faster and raises safety concerns.
Scientists like Xiao are trying to sidestep many of these problems with their cathode.
The PNNL team has also developed a process to grow high-performance crystals in molten salts — sodium chloride, common table salt — at high temperature.
What’s the advantage of a single crystal compared to a polycrystalline material?
Think of keeping your food cool while camping.
A solid block of ice melts much more slowly than the same amount of ice that comes in small cubes. The block is more resistant to damage from higher temperatures and other outside forces.
It’s similar with nickel-rich cathodes: An aggregate of small crystals is much more vulnerable to its surroundings than a single crystal under certain conditions, especially when there’s high nickel content, since nickel is prone to induce unwanted chemical reactions.
Over time, with repeated battery cycles, the aggregates are ultimately pulverized, ruining the cathode’s structure with micro-cracks.
Now, PNNL is working with the Albemarle Corporation, a major specialty chemical manufacturing company and one of the world’s leading producers of lithium for electric vehicle batteries, testing its nickel-rich cathode materials at kilogram scale.
Magnesium tipped as a future star
While lithium technologies rule today, scientists are working on various new generation batteries, including the promising, common element magnesium.
Magnesium batteries have long been considered a potentially more powerful, safer and less expensive alternative to Li-ion cells.
Magnesium is more abundant than lithium, has a higher melting point, forms smooth surfaces when recharging, and has the potential to deliver more than a five-fold increase in energy density if an appropriate cathode can be identified.
Development started in the 1990s but cracking the magnesium nut has proved tougher than with lithium and so magnesium batteries remain at least several years away in practical market terms.
The primary problem has been the lack of a suitable cathode, or positive electrode — otherwise known as the part of a battery where the magnesium ions enter during discharge of the battery to power an electronic device and then exit during charging.
We’re picking up the magnesium story in 2018 with a claimed breakthrough by a multi-institution team of scientists led by Texas A&M University chemist Sarbajit Banerjee.
The team had discovered what they said at the time was an “exceptional metal-oxide magnesium battery cathode material”, perhaps opening the door to a higher density of energy storage on top of transformative advances in safety, cost and performance in comparison to their ubiquitous Li-ion counterparts.
Curiously, the team’s solution was based on a redesigned form of an old Li-ion cathode material, vanadium pentoxide, which they proved was capable of reversibly inserting magnesium ions.
But, following the very public fanfare of February 2018, things have since gone rather quiet on the magnesium front at Texas A&M.
However, there has just been another and different breakthrough. Researchers at Houston University and the Toyota Research Institute of North America (TRINA) have developed a new cathode and electrolyte – previously the limiting factors for a high-energy magnesium battery – and come up with a magnesium cell capable of operating at room temperature and delivering a power density comparable to that offered by Li-ion batteries.
Magnesium ions hold twice the charge of lithium, while having a similar “ionic radius” and this lies behind the earlier poor power performance previously achieved at room temperature.
One approach to addressing this challenge is to improve the chemical reactions within a cell at higher temperatures. Another is to store magnesium cations – positively charged ions – in their complex forms. But neither approach is practical.
Yan Yao, Cullen Professor of Electrical and Computer Engineering at Houston says the new and “ground-breaking” results have been achieved through combining both an organic quinone cathode and a new tailored boron cluster-based electrolyte solution.
But although TRINA researchers are recognised as having made “tremendous advancements” in the magnesium battery field, including developing highly recognised, efficient electrolytes based on boron cluster anions, these electrolytes had limitations when it comes to supporting high battery cycling rates.
Put simply, the number of cycles for a rechargeable battery indicates how many times it can undergo the process of complete charging and discharging until failure or it starting to lose capacity, with the market demanding more cycles charging up at faster rates.
The new battery developed by Houston-TRINA is claimed to be almost two orders of magnitude higher than the power density achieved by previous magnesium batteries.
Moreover, it was able to continue operating for more than 200 cycles with around 82% capacity retention, showing high stability. The project team says it can further improve cycling stability with further work.
That work continues.