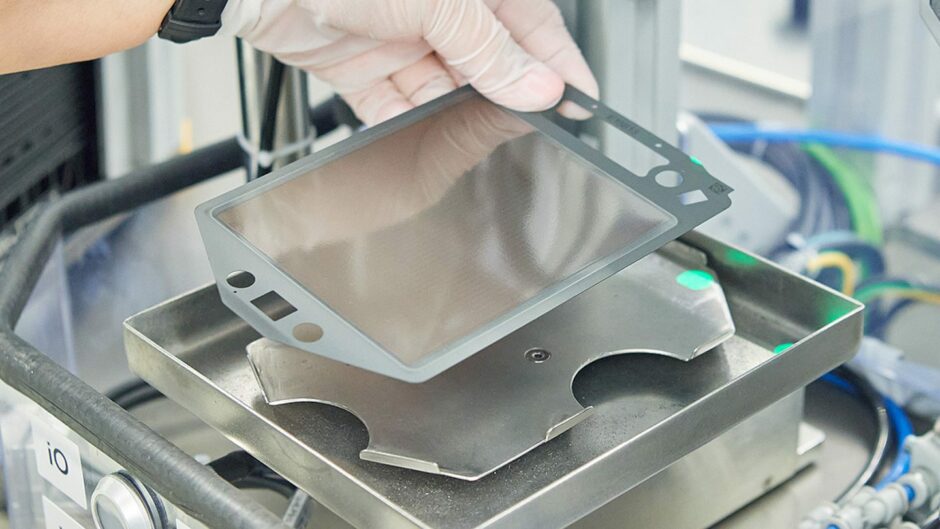
Hydrogen will unquestionably play a key role in the energy transition – but to do so will require the rapid expansion of equipment to produce, store, transport and consume it.
“What we have yet to really do in the hydrogen fuel cell world is scale – but scale up is a very difficult part of a business’ cycle,” noted Phil Caldwell, chief executive of hydrogen technology firm Ceres.
As he sees it, the problem for hydrogen technology developers and manufacturers is clear. “I’ve pursued this for the last 20 years and it’s very hard for pure play companies to invent the technology and scale it to have that impact.”
“The technology is only one piece of it; you need the supply chain strength, you need the balance sheet to build these gigafactories, you need the skilled service support and all the product development that goes with that.”
Eschewing those issues, UK-based Ceres has pursued a technology-only approach, developing a “unique” solid oxide technology that it licences to larger partners across the globe who have the capacity to handle scale up and manufacturing.
Unlike polymer electrolyte membrane (PEM) and alkaline systems which use liquid electrolytes, such systems use solid material to conduct negative oxygen ions from the cathode to the anode, where electrochemical oxidation of hydrogen, carbon monoxide or other organic intermediates by oxygen ions then occurs.
In Ceres’ case, this electrolyte is a ceramic printed on sheets of regular steel and assembled into “stacks”.
“It makes it a very low cost and highly manufacturable technology, but also it’s well protected with IP, which means we can actually operate a licencing business,” explains Mr Caldwell.
The technology is flexible, capable of running on gas, bio-gas, hydrogen, and various blends thereof – it can even run on future fuels and synthetic fuels, like methanol.
It’s also flexible in its outputs. Run one direction, solid oxide technology can act as a fuel cell to produce electricity; run in the other, it can act as an electrolyser, splitting gas or synthetic fuels to produce pure hydrogen.
Ceres is pursuing partnerships looking at applications for both.
Key partnerships
As Mr Caldwell makes clear, it’s partnerships that will allow Ceres’ technology to go mainstream. Headquartered in Horsham, West Sussex, the company employs around 600 people worldwide, but has ambitions that can only be achieved by companies many times larger.
“There are many companies now that are having to go through this energy transition,” he said, pointing to automotive and oil gas firms, among others.
“Very often they realise that the smaller companies don’t necessarily have the balance sheet or the capability to scale. What we do is licence technology, we help companies develop products and also build factories around production of our technology and then collect royalties,” he explained, likening the model to that of UK-based chip maker ARM.
Those partnerships now include the likes of Bosch, Doosan and Weichai, with agreements in place to set up plants with output in the tens, even hundreds of megawatts in Germany, South Korea and in China.
The energy sector is watching too. An agreement signed this year with supermajor Shell will see the two work to deliver a “megawatt-scale” solid oxide electrolyser (SOEC) demonstrator in Bangalore, India in 2023.
The system will be installed at Shell’s research and development technology centre in the city, where the hydrogen will be used in industrial processes on site. Ceres has said it will help it advance and commercialise the technology, with a view to achieving a “market-leading” levelised cost of hydrogen of $1.5/kg by 2025.
Even at that price, Mr Caldwell makes clear that Ceres’ solutions are not a silver bullet. PEM technology offers greater power density and can be used more dynamically – important if the equipment is going to be hooked up to variable renewable generation, like a wind turbine.
On the other hand, Ceres’ solid oxide approach offers scale and efficiency when used in the kinds of industrial applications where it can be most effective. Although it requires a higher operating temperature, that can be achieved using waste heat and steam from process industries, and in doing so push the efficiency “about 20 percentage points or more” above low-temperature alkaline and PEM systems.
“Particularly where energy markets are now, two-thirds of the cost is the actual energy input into it, so efficiency is really important in terms of hitting low-cost hydrogen,” he explained.
It makes the case, as he sees it, a “no-brainer” for large-scale applications.
Global aspirations
The partnership model goes against the grain of some proponents who would prefer UK technology be overseen and manufactured here.
Mr Caldwell isn’t against the idea – should the right partner materialise – but makes clear Ceres won’t be transforming itself into a homegrown manufacturer.
“[UK manufacturing] is a nice to have for our business, but it’s not essential… The scale and pace that we need for this energy transition, we have to be tackling the hardest challenges globally to be relevant and we want to get this technology out there on that scale.”
“If we were trying to do this ourselves, you might build a factory in the UK and then you might think about building factories somewhere else – but you’ve only got the bandwidth and the capability to do it one at a time.”
“Here we are able to be in the Korean market, the Chinese market, the European markets simultaneously because we’re collaborating and we’re leveraging our partners capabilities.”
Looking ahead, he sees the technology starting to gain traction by the middle of the decade, growing its market share “substantially” from there based on its competitive economics.
“What we’re doing now is developing partnerships to bring this technology into, if you like, the next generation of electrolysis,” he says. “From there we continue to scale up and grow them – gigafactory-scale production is our aspiration.”
Recommended for you
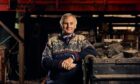