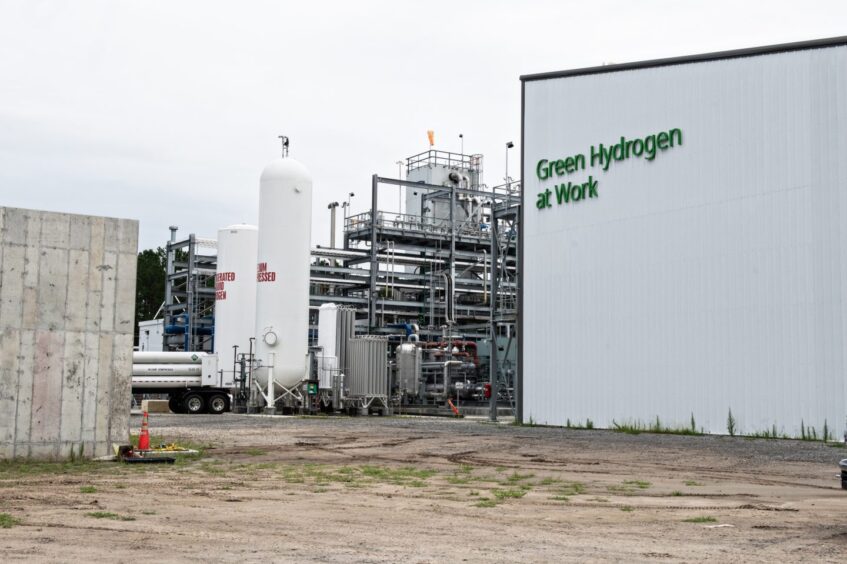
Hydrogen’s potential as a carbon-free fuel has provoked no end of excitement. From the deserts of Australia and Namibia to the wind-blasted straits of Patagonia, companies and governments worldwide plan to build almost 1,600 plants to make it. The gas can be produced cleanly by using wind- or solar-powered electricity in a process that splits the molecule from water. There’s only one problem: The vast majority of those projects don’t have a single customer stepping up to buy the fuel.
Among the handful with some kind of fuel purchase agreement, most have vague, nonbinding arrangements that can be quietly discarded if the potential buyers back out. As a result, many of the projects now touted with great fanfare by countries vying to become “the Saudi Arabia of hydrogen” will likely never get built. Just 12% of hydrogen plants considered low-carbon because they avoid natural gas or mitigate emissions have customers with agreements to use the fuel, according to BloombergNEF.
“No sane project developer is going to start producing hydrogen without having a buyer for it, and no sane banker is going to lend money to a project developer without reasonable confidence that someone’s going to buy the hydrogen,” says BNEF analyst Martin Tengler.
It’s easy to understand why hydrogen boosters see such potential. The molecule may be essential for the world to reach net-zero carbon emissions in the fight against climate change. When burned in a turbine or fed through a fuel cell, it generates energy without spewing greenhouse gases into the air. Almost all of it used today is stripped from natural gas, but producing it from water and renewables gives off no carbon at all.
Many analysts see no other way to decarbonize steel, maritime shipping and other industries that can’t easily run on electricity. BNEF predicts we’ll need to use 390 million tons of hydrogen per year worldwide in 2050 to eliminate carbon emissions from the global economy, more than four times the amount used today.
But it’s not a simple switch. Most of the businesses that could run on hydrogen would need expensive new equipment to use it, a leap they’re reluctant to make. Hydrogen produced using clean energy costs four times as much as hydrogen made from natural gas, according to BNEF. And it’s hard to build the infrastructure to supply hydrogen—not just plants to make it but pipelines to move it—when the demand may not materialize for years.
“It’s no different than any other energy development at scale. Natural gas pipelines didn’t get built without customers,” says Laura Luce, chief executive officer of Hy Stor Energy. Her company has an exclusive letter of intent to supply hydrogen to an iron mill that Sweden’s SSAB SA plans to build in Mississippi.
Countries with the potential to generate abundant renewable power, such as Chile with wind and Australia and Egypt with solar, have announced grand goals to make the fuel, often for export. More than 360 plants have been announced in China alone, according to BNEF.
The European Union has set a target of producing 10 million metric tons of carbon-free hydrogen by 2030 while importing an equal amount. In the US, President Joe Biden has devoted $8 billion to creating “hydrogen hubs,” clusters of businesses making and using the fuel.
Andy Marsh, CEO of Plug Power Inc., says his company has engineering and design work underway on European projects that together would use about 4.5 gigawatts of renewable power to generate hydrogen. “If half of it comes to fruition, we’ll be happy,” he says. “If a quarter of it comes to fruition, we’ll be happy.” Although the EU has set ambitious goals, Marsh says, member states are still incorporating them into their own regulations, delaying private investments.
In the US the industry and the Biden administration continue to haggle over the requirements for claiming hydrogen tax credits under federal law. Projects intended for export, meanwhile, face additional hurdles. Unlike natural gas or oil, a global system for shipping hydrogen doesn’t yet exist. Transporting hydrogen requires supercooling it, compressing it or carrying it in another, more manageable form such as ammonia, which combines hydrogen with nitrogen.
Werner Ponikwar, CEO of hydrogen equipment maker Thyssenkrupp Nucera AG, considers pipelines a good option, but many would-be hydrogen exporters wouldn’t be able to reach potential customers via pipe. “If you have to bridge an ocean, that’s more difficult,” he says. Many expect a quiet culling of more aspirational projects. Some proposed plants have already been shelved.
Ponikwar says those likely to succeed today are ones that include “the whole ecosystem,” locating a hydrogen plant near a clean energy source, with a ready customer close at hand. His company, for example, is supplying equipment to a hydrogen plant in northern Sweden that will in turn feed an iron and steel mill being developed by H2 Green Steel, which has secured €6.5 billion ($6.9 billion) in funding for the project. The region’s abundant hydropower will provide the electricity, and Mercedes-Benz Group AG has agreed to buy 50,000 metric tons of the mill’s steel per year. “With green steel, there’s a market that’s interested to buy, and they’re willing to pay a premium for it,” Ponikwar says.
Hy Stor took a similar path, designing a project that will be located near its customer SSAB. The company’s Mississippi project will use on-site wind and geothermal energy to produce the hydrogen, storing it in an underground salt dome. Other customers are now interested in the project’s hydrogen, Luce says. Although construction hasn’t begun, she aims to have the project up and running by 2027. “We didn’t build a project and then go and try to sell people on it. We built a project around a customer,” Luce says. “I do always think that customer-aligned projects find a way of getting built.”
Recommended for you
