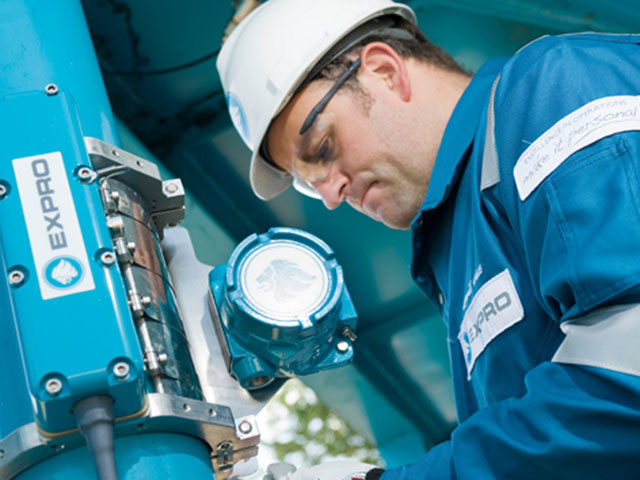
Expro are currently collecting real-time data to support production optimisation from brownfield wells using their non-intrusive wellhead surveillance technology.
With more than 70% of current world oil production coming from mature fields, the challenge in a low oil price environment is to extend the production life of these fields cost effectively.
The company’s clamp-on flow meters use sonar array processing to determine the rate at which naturally occurring flow turbulence, known as coherent vortical structures, travel past an array of sensors.
The meters, both PassiveSONAR and ActiveSONAR (analogous to passive and active underwater sonar methods) are seeing increasing industry acceptance for applications throughout the well lifecycle.
The surveillance service has already been applied in the North Sea by major operators to lead proactive decision making in the implementation of production optimisation campaigns.
The service is widely adopted in the Middle East as well for production surveillance, ESP optimisation, and gas lift and water injection optimisation.
John McKay, sales manager for Expro Meters, spoke on the technology at SPE Aberdeen’s Technical Presentation, held in the city last week.
He said: “A key part of production optimisation is to get a better understanding of the current state of the field’s production.
“Non-intrusive wellhead surveillance gives operators the ability to collect real-time data from individual wells without production interruption, at lower cost than traditional production testing methods whilst minimising safety risks associated with traditional well testing technologies.”
“This involves a holistic review of reservoir management, plant capacity wells and pipeline, optimisation tools, man power etc, to identify system bottleneck and opportunities to arrest the decline curve.
“Well testing frequency and duration, along with meters operating out of specification that were perhaps sized for early production, have been identified as two common hurdles to optimising production.”
The first successful field-wide surveillance for the technology was Centrica Energy’s operated North and South Morecambe Fields, which are among the largest in the UKCS in terms of original reserves.
Monitoring real-time production surveillance rates from each well in the field provides critical information for reservoir management and workover planning.
Centrica explored the range of potential replacement technologies for the existing venturi meters, including installing new in-line differential pressure meters of several types, as well as traditional ultrasonic type meters.
Turndown ratio, or the instrument’s measurement range, was an important consideration as this instrument was expected to measure well production throughout the declining life of the field.
After a trial to assess Expro meters’ applicability to well conditions in the Morecambe fields, the meters were subsequently permanently installed on all 44 producing wells across six platforms (SonarMonitor).
Sonar meters clamped onto the existing pipework allowed installation without shutting in the well (and incurring the associated lost production) reducing management of change and HSE exposure.
With the installation of sonar flow meters, production teams were able to benefit from the availability of real-time flow information for each well.
Following the start-up of a new, high pressure field, wells on one of the platforms had reduced in performance. Sonar flow meters were used to establish the worst affected wells, along with those that would respond well to a cycling procedure.
The decision was made to have a particular well shut-in for an hour each day, in order to help unload liquid in the tubing and achieve slightly higher flow rates from the well. The benefit was observed almost immediately, with peak flow rate almost doubled. Further shut-in lengths and/or frequencies were implemented on the well until an optimum operating routine was established.
Expro have conducted individual well surveillance on the Marathon-operated East Brae platform. In this case, the technology is deployed as a service whereby the sonar meters and Surveillance Technicians are deployed periodically to collect and report production data (SonarTest).
Prior to sonar surveillance, wells capable of only flowing to the platform’s low pressure (LP) production separator needed to be shut-in to allow individual well tests. Wells can now be individually sonar well tested without production interruption with different methods adopted to optimise production and combat liquid loading.
‘Swing’ wells use the LP separator to unload liquids and thus improve their subsequent performance in the platform’s high pressure separator.
Sonar metering determined the optimal cycle frequency for individual wells, allowing the operator to keep the separator full and maintain maximum rates in the HP separator. This intensive well management has assisted in reducing the production decline of the East Brae field.
McKay added: “Sonar testing can have a major impact in aiding production allocation from individual wells enabling engineers to identify underperforming areas and implement short and long-term strategies such as well cycling.
“Sonar flow surveillance data can then be used to evaluate the effectiveness of this work and select suitable candidates for further intervention work, helping to prolong the field life of a mature asset.
“In this current challenging market for our clients, where capital expenditures available for new equipment are limited, clients appreciate that we can deploy personnel and clamp-on sonar metering equipment on a schedule that works for their surveillance needs and budget. The client pays for data as an operating expense rather than taking on a capital project.
“Looking to the future, sonar metering technology will continue to deliver non-intrusive surveillance solutions that deliver critical data and enable operators to make important decisions for the well lifecycle.”
Recommended for you
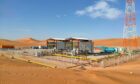