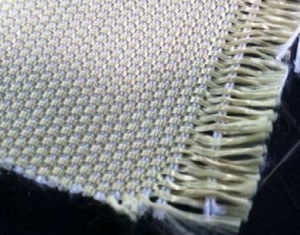
A new “bomb proof” fabric is being used by North Sea oil and gas companies to save millions of pounds by cutting down time during pressure testing operations.
Xtegra is a sophisticated yarn that gains extrordinary strength from the way the yarn is created.
Houston-based technology firm AFT has developed the fabric which uses a combination of fibres to create an “auxetic” yarn which when stretched becomes thicker rather than thinner. This gives Xtegra the strength to contain powerful explosions.
Xtegra is made with synthetic fibres including DuPont’s Kevlar and a rubbery, plastic called Hytrel.
Shrapnel from an explosion bounces off the fabric as it stretches and thickens to absorb the kinetic energy and then snaps back.
The company has developed configurable fire-resistant curtains that are used to protect personnel and high-value assets. The curtains are capable of containing a blow out up to 25,000psi.
The curtains are non-structural and portable, and can be quickly configured and installed on a rig or platform during pressure testing procedures offshore. This allows for the rigs to minimise or avoid shut down and enables operators to continue drilling through the 21-day test periods.
A case study with Total saw two blast curtains installed on Rowan Drilling’s Rowan Gorilla V rig last year.
The curtains were installed on the drill floor to isolate the stand pipe manifold and the choke manifold. The curtains are on fixed rails so can be opened out and extended easily and secured away when not required.
It allowed high pressure testing on the two manifolds while work was performed on the drill floor, leading to a time and cost saving of more than half a million pounds over the course of just six BOP tests.
Aberdeen-based service company Screw Conveyor has secured a global licensing agreement with AFT to deploy the Xtegra blast curtains offshore.
“Rigs have a congested drill floor so being able to perform operations simultaneously while manifold pressure testing is being carried out has brought significant savings,” said sales manager John Dudgeon.
“The manifolds are on drill floor and are under high pressure right next to the area where drill crew are working. It means work is typically stopped during a choke manifold test.”
“The blast curtains allow the operations to start again as soon as the BOP itself is entirely tested and the test string is out of the hole, because the rest of the choke manifold tests are performed behind them, protecting the crew on the drill floor.”
It means that rig operators can save as much as one rig day every month. One major drilling contractor estimated that it could save up to $4million a year by using the curtains, said Dudgeon.
Dudgeon added: “Although pressure testing is not classified as Non Productive Time (as pressure testing is not considered as non productive), the curtain doesn’t “avoid down time” but rather increases the efficiency of the overall operation.”
In a test carried out by the British Ministry of Defence, five 1mm layers of Xtegra stopped shrapnel from a rocket-propelled grenade detonated five metres away.