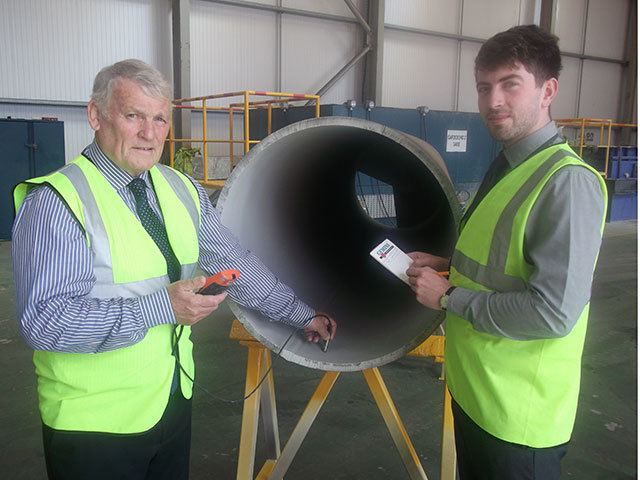
A Scottish company that has made a significant success out of the development and application of anti-corrosion coatings to oilfield tubulars has developed what could prove an industry game-changer.
Montrose-headquartered Gemini Corrosion Services has come up with what it says is a way of effectively applying well proven, aluminium-based long-life, hot-spray coatings to the inside of pipeline tubulars as a continuous process.
The hope is that, once the offshore industry gets to hear about the technology, the Scottish company really will be able to operate as a total one-stop tubulars shop out of Montrose.
Gemini was established in Stonehaven during 1982, but migrated its business to the Mearns seaport in 1999 for a variety of sound business reasons including lower land costs and ample space for growth.
Founder and managing director of the company, Ian Guthrie, said there is nothing new about the long-life aluminium coatings applied thermally . . . they are thoroughly proven and heavily used worldwide on the exterior of tubulars.
This process is known as TSA and the result is a very durable finish with a service life of 25 years or so. That is far better than any painted system developed to date and Gemini invested in an automated TSA plant as a part of the move to Montrose.
Nor is there anything particularly new about the TSA spray heads; like the coating itself, they are thoroughly proven.
What is novel with the Gemini system is the way in which the spray heads have been set up for working inside tubulars and the manner in which sections of pipe are simultaneously rotated and transported during spraying to enable a consistent coating thickness prior to a sealer being applied.
Work on that aspect of the system is ongoing and has been given a boost by at least two steel tubulars manufacturers taking a close interest.
“We’re working with a variety of different sealers, one of which is significantly smoother after finishing than stainless steel,” said Guthrie.
The sealer system helps make the inside of coated tubulars more slippery to fluids passing through, plus it adds to the protection against corrosion.
Gemini is currently equipped to routinely handle external TSA of tubulars ranging from nine to 50 inches in diameter and of varying lengths.
The plan now is to adapt the newly developed interior spraying capability to handle this portfolio of standard sizes, including right down to four-inches diameter.
As Guthrie explained to energy, the Gemini process opens the door to a long-life coating system inside tubulars without the need for more expensive solutions such as stainless steel liners.
“We’re much cheaper,” he said. “The issue for us was finding a way of achieving a smooth TSA coating on the inner surface of tubulars and we’re now achieving that.
“It helps that everyone has confidence in TSA as it’s such a well proven process.”
Guthrie has had a working dialogue with the Welding Institute in Cambridge throughout the development process.
Given the impact that the new internal TSA system could have on the business which currently employs just over 30 people, he added that discussions with possible future potential partners would be welcome.