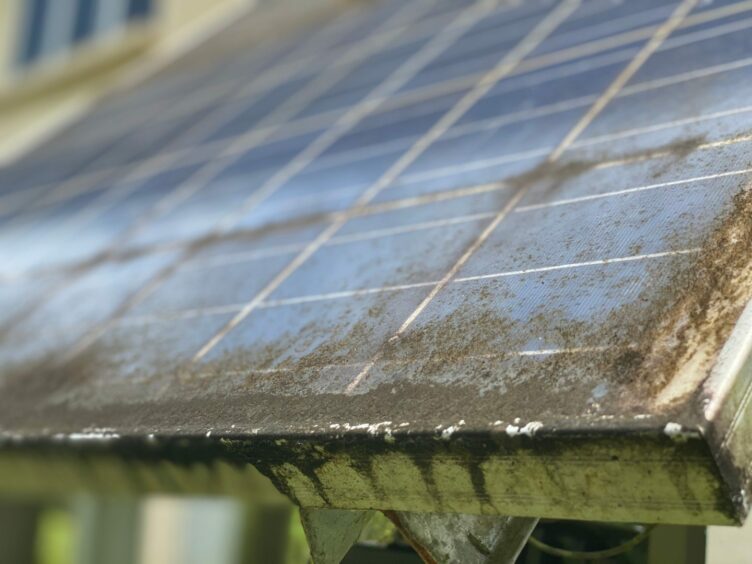
Solar panel technology has come a long way over the past 40-50 years, however, it is clear that effective, comprehensive global recycling is not.
In the US alone, tens of millions of panels are being installed annually, which suggests that the global figure is well north of 100million panels installed annually. But hardly any operational recycling facilities exist … two only in the “Sunshine State” California by 2022.
In the All-Energy diaspora, photovoltaics command massive attention and are highly flexible in terms of their application and relatively low cost.
They are ubiquitous; from gigawatt class solar farms to the roofs of large corporate buildings and car parks generating hundreds of kilowatts of urban power, to millions of homes with around 5kw of generating capacity apiece, to a single panel and a car battery revolutionising life for villagers in remote, poor communities scattered across all continents.
The Golmud Solar Park in China is the world’s largest solar farm with an installed solar capacity of 2.8GW generated by nearly seven million solar panels; but with an eventual capacity boost to 16GW over the next five years or so.
To put that into context, one gigawatt can power one million UK homes for an hour, or around 100 million LED light bulbs.
All share a common problem: eventual disposal. And, while there are examples of over 90% recycling efficiencies being achieved in some flagship disposal facilities such as in France, countless millions have simply been dumped in landfill with no let-up in sight.
The cumulative value of materials that can be recycled from solar photovoltaic (PV) waste in a 1.5°C global temperature increase scenario is estimated at $4billion by 2040 and $8.8billion by 2050, according to the preliminary findings of a new joint study undertaken the International Renewable Energy Agency (IRENA) and US Department of Energy’s National Renewable Energy Laboratory (NREL).
Silver, copper and aluminium will form the largest share of materials by value that can be recycled, according to Jinlei Feng, one of the authors of the forthcoming report ‘End of Life Management of Solar PV in the Energy Transition – Enabling circular economy’.
Speaking at the IRENA 13th Assembly in January, he said more than 100 gigawatts (GW) of new solar capacity was added in period 2019 to 2021 and alone lead to a major jump in waste generated in about 25 years.
“For crystalline silicon solar PV technology, there will be demand for materials like glass, aluminium paste and aluminium frames and silver. Silver accounted for 9% of materials required by value for global annual solar PV production in 2020 alone,” said Feng.
“By 2050, there will be more than 210 million tonnes of cumulative solar PV waste globally and more than three quarters of that waste will be generated after 2040 and 40% in the last five years between 2045-2050.
“Annual solar PV waste generation will touch 10 million tonnes by 2040 and increase to 20 million tonnes by 2050.”
He said very few countries have programmes to support development of PV recycling as part of circular economy dream and that policies, programmes and collaborations among stakeholders is urgently needed.
As of today, it seems only one 100% recyclable panel has so far been introduced to the market. It is the work of Dutch PV manufacturer Solarge, which claims that a “paradigm shift is now needed to harvest the full potential of solar energy”.
Solarge, together with EconCore (also Dutch), a manufacturer of honeycomb sandwich material, were due to launch at JEC World 2023 (April 25-27) a new fully circular (recyclable) solar panel while also reducing weight by up to 65% for rooftops.
Today there are two mainstream types of solar cells though a third appears close to market. Life expectancy of each family type is generally estimated to be around 20 years.
The most common is silicon-based and accounts for 90% of the current market.
The other type is called thin-film solar, which in turn uses three main sub-technologies, one of which is known as CIGS (copper, indium, gallium, selenide), and consists of a layer of different metals, including indium and silver. Thin-film solar cells are by far the most effective of today’s commercially available technologies.
They can also be made bendable and adaptable, which means that they can be used in many different areas. The problem is that the demand for indium and silver is high, and increased production is accompanied by increasing waste, which contains a mixture of valuable metals and hazardous substances.
Being able to separate attractive metals from other substances, therefore, becomes extremely valuable, both economically and environmentally, as they can be reused in new products.
The third PV family (PSCs), now in the early stages of commercialisation, is based on perovskites, which are a group of crystalline minerals with semiconductor properties that may, in future, be used for solar cells because they are flexible, lightweight and cheap.
Perovskite materials, such as methylammonium lead halides and all-inorganic caesium lead halide, are not just cheap to produce, they are also simple to manufacture.
PSCs offer the potential of being significantly more efficient than silicon and thin-film systems; and the very nature of their composition appears to point towards greater recyclability…materials recovery.
At last, increasingly serious money is being directed into PV recycling research. Its potential as a key part of the energy circular economy that by and large continues to elude should be enormous.
Our first example of current PV recycling research concerns the need to find a more efficient, environmentally responsible way of recovering precious metals from thin-film solar cells.
According to a team of researchers at Chalmers University of Technology, Sweden, the methodology they’re developing will also pave the way for more flexible and highly efficient solar cells.
“It is crucial to remove any contamination and recycle, so that the material becomes as clean as possible again. Until now, high heat and a large amount of chemicals have been used to succeed, which is an expensive process that is also not environmentally friendly,” says Ioanna Teknetzi, a Chalmers PhD student.
“We took into account both purity and environmentally friendly recycling conditions and studied how to separate the metals in the thin-film solar cells in acidic solutions through a much ‘kinder’ way of using a method called leaching.
“We also have to use chemicals, but nowhere near as much as with previous leaching methods.
“To check the purity of the recovered indium and silver, we also measured the concentrations of possible impurities and saw that optimisation can reduce these.”
The team have demonstrated that it is possible to recover all of the silver and (so far) about 85% of the indium.
The process takes place at room temperature with no need for adding heat. It takes one day, which is slightly longer than current processing methods but is claimed to be more cost-effective and environmentally acceptable.
Meanwhile, on the other side of the planet, a microwave technology invented at Macquarie University in Australia is predicted to improve the manufacture of silicon-based solar cells whilst also make them easier to recycle.
During the fabrication of solar panels, silicon goes through several high-temperature processes known as annealing. Currently the cells are cooked in an oven.
But the Macquarie team, led by senior lecturer Dr Binesh Puthen Veettil of the School of Engineering, has shown that heating using microwave radiation is nearly as efficient. Plus, it saves considerable time and energy and has other advantages.
Because microwave radiation can selectively heat silicon, it leads to almost instantaneous effects with massive savings of energy apparent.
According to Dr Veettil, under microwave treatment, the plastic (ethylene vinyl acetate) coating that protects a PV panel’s silicon plate from moisture and contamination softens to the point where it can be peeled off mechanically. That means the plate can be easily delaminated and its components reused without employing harsh chemicals.
“Until now it made economic sense to just dump the panels in the landfill,” says Dr Veettil. “In the rare instances when they are recycled, you crush the panels, heat them to about 1400°C and wash them with chemicals to remove the plastic – a highly energy-demanding process.
“But now, as the solar panels which began to be installed in vast numbers about 20-30 years ago are reaching the end of their life and being decommissioned, governments are demanding they be recycled.”
Coincidentally, there are several other projects involving solar cells and sustainable energy underway at Macquarie, including experimenting with the application of microwave annealing when building perovskite solar cells.
In this case, the microwave radiation produced more efficient solar cells as compared to conventional annealing methods, but the reason is not clear. The current work is being undertaken partly to answer that question.
Recommended for you
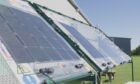