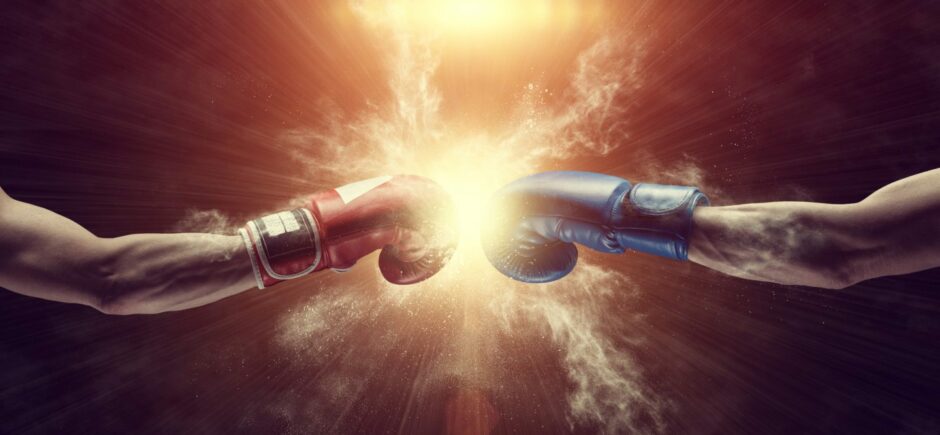
The low carbon energy revolution has become an unstoppable juggernaut as acceptance grows that the threat of catastrophic global climate change must be brought under control.
However, with the exceptions of hydro-power and, to some extent, fuel cells, the dominant low carbon solutions on offer – primarily wind and solar power – are not yet able to deliver reliable electricity because of the lack of copious, low-cost back-up energy storage capacity; basically the chemical battery, but not as we currently know it.
And that in itself can take variety of forms and not just the familiar, good old lead-acid battery; Li-ON (lithium ion) battery packs in EVs (electric vehicles); ubiquitous consumer cells from the supermarket – usually lithium or silver oxide cells; not forgetting fuel cells.
A huge global effort is under way to find high efficiency, low-cost and long-term alternatives to the current offerings and to drastically improve what we have.
The basic question is, will lithium-ion remain the dominant battery technology in the automotive sector and other industries, or will other chemistries take over?
For now the big money is on Li-ON which, though it has serious shortcomings, is where the big money is currently being placed.
BP is a good example as it plans to invest as much as $60 million in a new EV battery test centre and analytical laboratory in the UK. Due to open by the end of 2024, the new centre is to be located at energy super-major’s existing global HQ for its Castrol business at Pangbourne in Berkshire, where it undertakes R&D of fuels, lubricants and EV fluids.
BP says the new facilities will help advance the development of leading fluid technologies and engineering for hybrid and fully battery electric vehicles, aiming to bring the industry closer to achieving the key tipping points for mainstream electric vehicle (EV) adoption. Castrol has been working on advanced EV fluids designed to manage temperatures within Li-ON cells to enable ultra-fast charging and better efficiency.
Meanwhile, in its so-called Big Battery Challenge, the UK’s Institute of Mechanical Engineering (IMechE) experts have determined that, while it is likely the Li-ON battery will dominate for the time being, “there are plenty of potential long-term challengers”.
Contenders
Three contenders are especially identified: sodium ion (Na-ON), solid state and Lithium-sulphur (Li-S).
Sodium-ion batteries are regarded as an emerging technology with “promising cost, safety, sustainability and performance advantages” over commercialised lithium-ion batteries.
According to IMechE material: “Key advantages include the use of widely available and inexpensive raw materials and a rapidly scaleable technology based around existing Li-ON production methods. These properties make Na-ON batteries especially important in meeting global demand for carbon-neutral energy-storage solutions.”
The development of solid-state batteries that can be mass manufactured is one of the most important challenges in the industry today, reports the IMechE.
“The ambition is to develop solid-state batteries, suitable for use in electric vehicles, which substantially surpass the performance, safety and processing limitations of Li-ON batteries,” it states.
“In contrast to research into Li-ON batteries, which will provide incremental gains in performance towards theoretical limits, research into solid-state batteries is long term and high risk but also has the potential to bring high rewards.”
And thirdly, Li-S, which too is claimed to offer cheaper, lighter batteries with safety advantages. After initially finding use in niche markets such as satellites, drones and military vehicles, this chemistry is also thought to be capable of transforming aviation in the long term.
“Electric aircraft offering short-range flights or vertical take-off and landing (including personalised aviation and flying taxis in cities) are distinct possibilities by 2050,” notes the IMechE.
The institution adds: “The UK, which is already home to established lithium-sulphur battery manufacturers and to leading academics in the field, has a great opportunity to become the global leader in this ground-breaking technology.”
However, the above are not the only significant contenders for the great chemical battery storage prize. There are other wannabes that could give Li-ON and the trio above a run for their money.
Aluminium Sulphur
Take the work being conducted at the Massachusetts Institute of Technology in the US where an extended team of researchers at MIT itself and other institutions elsewhere have developed a new kind of battery, made entirely from abundant and inexpensive materials.
Their battery architecture utilises aluminium and sulphur as its two electrode materials, with a salt electrolyte as the medium.
In a paper by MIT Professor Donald Sadoway, along with 15 others at MIT and in China, Canada, Kentucky, and Tennessee, Sadoway says: “I wanted to invent something that was better, much better, than Li-ON batteries for small-scale stationary storage, and ultimately for automotive.”
Crucially, this includes dealing with a dangerous aspect of Li-ON technology … overheating and fire.
Besides being expensive, lithium-ion batteries contain a flammable electrolyte, making them less than ideal for transportation.
Sadoway started from basics by first studying the periodic table, looking for cheap, Earth-abundant metals that might be able to substitute for lithium.
According to the professor, the commercially dominant metal, iron, doesn’t have the right electrochemical properties for an efficient battery.
But the second-most-abundant metal in the marketplace … and actually the most plentiful metal on Earth … is aluminium. So the decision was made to us Al as a “bookend” electrode.
The next challenge was working out what to pair the aluminium with for the other electrode; then consider what kind of electrolyte to put in between to carry ions back and forth during charging and discharging.
According to Sadoway, the cheapest of all the non-metals is sulphur, so that became the second electrode material.
As for the electrolyte, the decision was made, not to use volatile, flammable organic liquids that have led to dangerous fires in cars and other applications of Li-ONion batteries.
The team tried various polymers but ended up looking at a variety of molten salts that have relatively low melting points … close to the boiling point of water.
“Once you get down to near body temperature, it becomes practical” to make batteries that don’t require special insulation and anticorrosion measures,” says Sadoway.
The three ingredients the MIT team ended up with are cheap and cannot burn.
In their experiments, they showed that the Al-S cells could endure hundreds of cycles at exceptionally high charging rates, with a projected cost per cell of about one-sixth that of comparable Li-ON cells.
They showed that the charging rate was highly dependent on the working temperature, with 110degC (230degF) showing 25 times faster rates than 25degC (77degF).
Surprisingly, the molten chloro-aluminate salt the team chose as an electrolyte simply because of its low melting point turned out to have a fortuitous advantage.
One of the biggest problems in battery reliability is the formation of dendrites, which are narrow spikes of metal that build up on one electrode and eventually grow across to contact the other electrode, causing a short-circuit and hampering efficiency. But this particular salt, it happens, is very good at preventing that from happening.
The team has come to the present view that their new Al-S battery should be “ideal for installations of about the size needed to power a single home or small to medium business,” producing in the order of a few tens of kilowatt-hours of storage capacity.
But there’s another application that the MIT team reckons its invention might also be ideal as energy buffer storage at busy EV charging stations.
Sadoway says that, when EVs become common enough that several cars want to charge up at once at a refuelling/recharging forecourt.
Fast charging eats amps and presently poses power supply challenges, therefore limiting the number of cars that can charge up at any one time.
“Having a battery system such as this to store power and then release it quickly when needed could eliminate the need for installing expensive new power lines to serve these chargers,” he adds.
The Al-S technology is already the basis for a new spinoff company called Avanti, which has licensed the patents to the system.
Calcium perhaps?
Scarcity, high prices, and safety issues associated with Li-ON cells is also the driver behind work being carried out on a calcium based battery at the Rensselaer Polytechnic Institute based in New York State.
They too argue that their proposition offers a greener, more efficient, and less expensive energy storage alternative. Calcium is already extensively alloyed with lead in lead-acid traditional batteries.
Dr Nikhil Koratkar uses the same basic materials argument as his MIT counterparts … abundance and low cost, but recognises that Li-ON sets the “gold standard in terms of performance”.
“However, lithium is a limited resource on the planet, and its price has increased drastically in recent years. We are working on an inexpensive, abundant, safe, and sustainable battery chemistry that uses calcium ions in an aqueous, water-based electrolyte.”
The Rensselaer team say they have been able to overcome issues associated with the use of calcium, notably the challenge of “inserting calcium ions into the battery electrodes.
“We overcome this problem by developing a special class of materials called molybdenum vanadium oxides (MoVO) that contain large hexagonal and heptagonal shaped channels or tunnels that run through the material,” says Koratkar.
Like the MIT team, he is optimistic: “Calcium-ion batteries might one day, in the not-so-distant future, replace Li-ON technology as the battery chemistry of choice that powers our society.
“This work can lead of a new class of high-performing calcium-based batteries that use Earth abundant and safe materials and are therefore affordable and sustainable.
“Such batteries could find widespread use in portable and consumer electronics, electric vehicles, as well as grid and renewable energy storage.”
Chilling out with Li-ON
Meanwhile, all sort of work continues around to globe to improve lithium batteries. For example, Li-ON batteries don’t like getting cold. EV and mobile phone performance is slashed, much to the annoyance of their users.
The problem is that, when temperatures drop below freezing, lithium battery anodes “get sluggish” and quickly give up.
To improve electrical performance in the extreme cold, researchers from a consortium of Chinese universities have replaced the traditional graphite anode in a Li-ON battery with a “bumpy” carbon-based material, which maintains its rechargeable storage capacity down to minus 31degF (minus 35degC).
They have worked out that the flat surfaces nature of graphite used in the manufacture of anodes is responsible for the drop in a lithium-ion battery’s energy storage capacity in the cold.
Lithium batteries are great for powering rechargeable electronics because they can store a lot of energy and have long lifespans.
But when temperatures fall below freezing they lose their ability to hold charge.
It is, for example, why many EV drivers in countries where winters are harsh experience transportation difficulties. It is also risky to use Li-ON batteries in space exploration.
To create the new material, the researchers heated a cobalt-containing zeolite imidazolate framework (known as ZIF-67) at high temperatures.
The resulting 12-sided carbon nanospheres had bumpy surfaces that demonstrated excellent electrical charge transfer capabilities.
Then the team tested the material’s electrical performance as the anode, with lithium metal as the cathode, inside a coin-shaped battery.
The anode demonstrated stable charging and discharging at temperatures from 25degC (77degF) to minus 20degC (minus degF) and maintained 85.9% of the room temperature energy storage capacity just below freezing.
In comparison, Li-ON batteries made with other carbon-based anodes, including graphite and carbon nanotubes, held almost no charge at freezing temperatures.
When the researchers dropped the air temperature to minus 35degC (minus 31degF), the anode made with bumpy nanospheres was still rechargeable, and during discharge, released nearly 100% of the charge put into the battery.
Incorporating the bumpy new nanosphere material into Li-ON batteries could open up the possibilities for using these energy sources at extremely low temperatures, the researchers say.
The scientists continue with their work; meanwhile paths to market research is also under way in China.
The consortium behind the work comprises: Central Universities (China), the National Natural Science Foundation of China, the Ministry of Science and Technology of China, the Science and Technology Project of Guangdong Province, the Chemistry and Chemical Engineering Guangdong Laboratory and Beijing Jiaotong University.