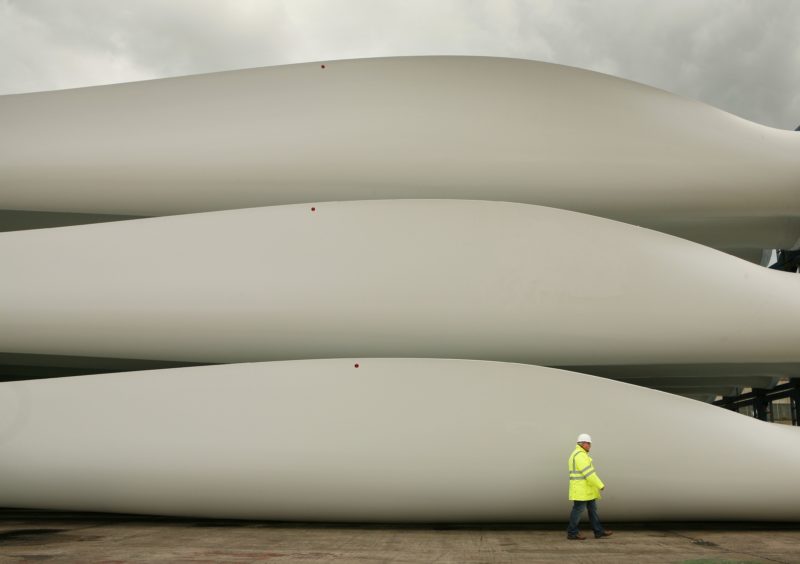
At-scale recycling of wind turbine blades could present the UK supply chain with “huge economic opportunities”, according to a new report.
The Offshore Renewable Energy (ORE) Catapult is calling for increased investment and a “radical shift” in research and development into the process after its study, carried out in collaboration with OGTC, found a “circular economy approach” in offshore wind could create an extra 20,000 jobs.
Currently, wind turbines are around 85% to 90% recyclable.
However, the blades, which are made from composites of resins and fibres, are “challenging” to break down, process and recycle.
ORE Catapult described them as the last “major hurdle” to achieving full recyclability.
The report, entitled ‘Sustainable Decommissioning – Wind Turbine Blade Recycling’, has identified 14 technologies that show promise for recovering blade material, though “further work” is needed before they can be deployed at scale.
In the coming years the first generation of wind farms will begin to “reach the end of their service life”, posing a serious issue to developers.
It is estimated that the global offshore wind industry will need to decommission 85 gigawatts (GW) of capacity – including 325,000 blades – by 2050.
While this provides an enormous challenge, it also illustrates the “scale of the future global market” for circular economy pioneers.
To ensure the “golden opportunity” materialises, the report says collaboration with the oil and gas industry, which uses composites in pipes, will be “crucial”.
Chris Hill, director of operational performance at ORE Catapult, said: “As the report makes clear, we are on the cusp of a break-through composites recycling solution.
“The technologies exist, but to be viable, they require intensified investment and some new approaches to studying and addressing the remaining innovation challenges.
“Engagement with the UK supply chain is the first step for us: recycling is only of benefit when the recovered materials have saleable end-products that prevent deployment of virgin materials.”
“Wind industry manufacturers and operators are beginning to set ambitious targets for achieving zero waste turbines within the next twenty years.
“There is also an active hotbed of research into lifetime extension of turbines, pushing towards 40-year lifetimes, as well as exploring alternative materials to composites.
“Recycling these first-generation blades is the first step in achieving zero waste, and as the report highlights, it can also be a stepping-stone to a spin-off circular economy.”
The report also included input from Leeds University and the National Composites Centre and was commissioned to investigate alternatives to landfill and incineration for end-of-life wind turbine blades.
The next phase of the project will assess and appraise glass fibre recycling processes in order to identify the “best” potential solutions for further study and demonstration.
ORE Catapult has targeted an at-scale demonstration of blade recycling in the UK within the next five years.
Dr Anne Velenturf, a research impact fellow at Leeds University who is leading research on a circular economy for offshore wind, added: “A high-value circular economy, in which wind turbines are designed for durability and for repair, reuse and remanufacturing ahead of recycling the materials, has a high potential to minimise carbon emissions and to open new business opportunities for companies in the UK, creating thousands of jobs in our communities.”
Recommended for you
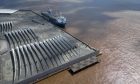