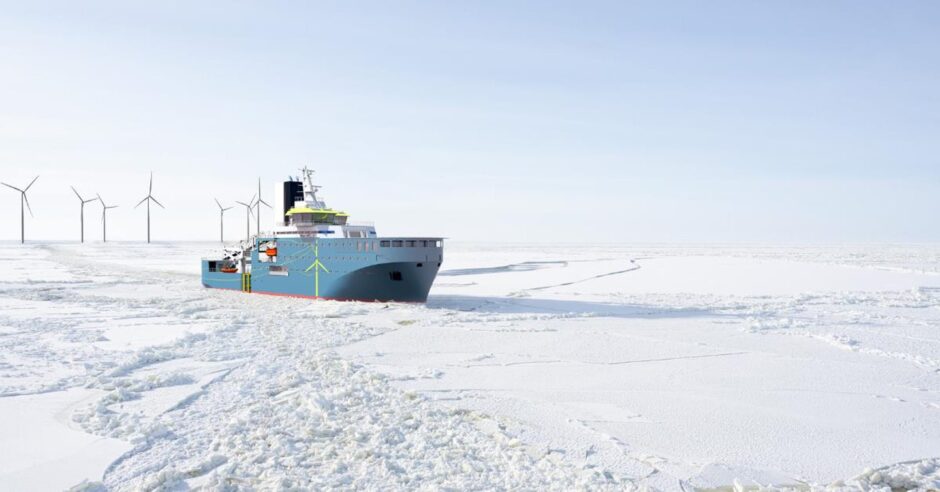
In June 2021, Team Renewable Arctic Finland launched a research call based on the need for ice research to better understand the sea ice loads affecting offshore wind farms.
They said VTT, one of Europe’s leading research institutions and pioneer in ice research, had tentatively agreed to lead the project, confirming the intent shortly after.
It would be turbine-centric and one of the main tasks would be to assess met-ocean conditions to improve the understanding of ice conditions and forces such as ice ridges and moving ice that offshore windfarm planted in areas like the northern Baltic would have to withstand.
And the project would eventually support the planning of a full-scale demonstration of offshore wind turbine in icing conditions.
Not in the brief, there was also the issue of developing ships capable of building and servicing icebound offshore windfarms.
This separate but related challenge was picked up by Finland’s Aalto University and other parties.
According to researchers at specialist shipping services provider Clarksons, as the offshore wind industry begins to expand in Arctic regions, the Baltic Sea will become a hotspot.
“By 2030, more than 1,000 turbines with a capacity of over 15GW are expected to be installed within the ice borders of the northern Baltic Sea including Sweden, Finland, Latvia, Lithuania and Estonia,” says Clarksons in a recent note adding that this would require ice-capable service vessels.
It happens that Clarksons has an SOV Concept and Design team which was hired by Finnish/Norwegian-owned Aker Arctic of Helsinki to support the development of the first ice-class windfarm vessel.
Out of this cooperation has emerged the ARC 311 vessel design.
Just as Aker Ice does with icebreakers, it will be possible to tailor the 84.4m ARC 311 to suit a specific operational area.
It has been designed to reliably reach ice-bound turbines no matter the weather and ensure year-round safe accessing and servicing.
As a result, Aker Ice says operators should find it easier to estimate windfarm maintenance and investment costs in seasonally freezing seas like the Baltic.
ARC 311 is based on Aker Arctic’s proven Double Acting Ship (DAS™) principle, meaning that class members will have an ice-going bow and icebreaking stern.
It is the basis of all current Finnish Icebreakers including two that were hybridised for North Sea oil and gas support – Fennica and Nordica.
Given the company’s extensive experience, including developing a number of shallow-drafted DAS vessels for service in the Baltic, large icebreakers for Russia; double-acting shuttle tankers like the Mikhail Ulyanov and Kirill Lavrov for the North-East Passage around the top of Russia, and a fleet of ice-breaking tugs for China, Aker Ice is confident that the cost of building its design can be contained.
Preliminary estimates suggest the ARC 311’s build price will come in around 5–10% higher than a similar-sized open-water model.
Aker Ice says the primary objective was to develop a ship as close as possible to an open-water service vessel, yet also capable of safe, independent, year-round operations without incurring high additional costs or increased fuel consumption.
According to Chief Designer Lars Lonnberg, employing the DAS™ principle – where the vessel advances bow-first in open water and light ice, and stern-first in heavy ice – has been crucial in creating an energy-efficient design.
“With our experience in designing efficient ice-going hulls, we have developed a stern form that breaks ice without using unnecessary power, thus avoiding excessive fuel usage,” adds project manager Juuso Lindroos.
They say that ARC 311’s ice strengthening and classification are suitable for operations across the entire Baltic, including the Bay of Bothnia, where winter conditions are the most severe.
The final ice-going capability of a vessel will be determined based on the operational conditions in the target area, with the design tailored accordingly.
There will be a lot that is familiar to rank-and-file SOVs and the ARC 311 has been designed to be just as adept.
A motion-compensated gangway is the safest means of accessing the turbines, and features such as midship location and winterisation have been included.
A passive roll damping system should ensure easy vessel movements in waves, enhancing safety and comfort for the crew.
Internal logistics and material handling have also been given attention with a view to minimising onboard personnel exposure to harsh Arctic conditions.
Aker Ice points out the choices in propulsion and fuel significantly affect energy costs, but also crew well-being. So, a hybrid solution is offered.
For in-farm operations, the ship will utilise electric propulsion and be able to plug in at the wind farm to charge batteries.
For shore-to-farm and other longer transits, diesel engines capable of burning alternatives such as methanol or ammonia will be the choice.
A retractable thruster, quieter than fixed tunnel thrusters, is also part of the low-noise solution.