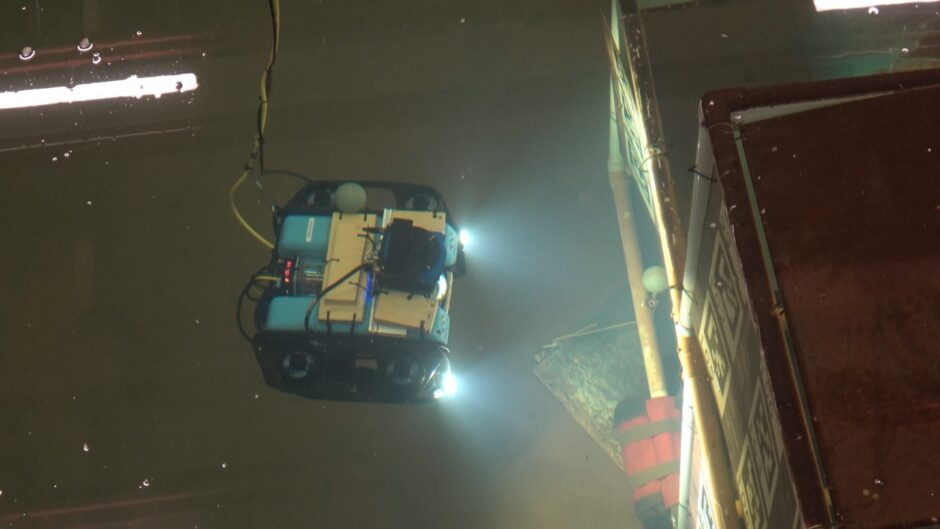
A £1.4 million research project at the National Robotarium has shown “promising results” in an effort to design fully-autonomous robots to fix offshore wind farms.
The project is developing artificial intelligence (AI) and control systems for the subsea robots which could “dramatically reduce the need for large maintenance vessels”.
The researchers said this could potentially reduce costs associated with maintenance for offshore wind farms, in addition to reducing fuel consumption by up to 97%.
It could also improve safety by reducing the need for personnel to work in hazardous environments offshore.
Based at Heriot-Watt University in Edinburgh, the National Robotarium trials form part of the UNITE project.
National Robotarium project manager David Morrison said the trials could “significantly lower both operational costs and the carbon footprint of maintenance” for offshore wind developers.
“Our trials are showing promising results in enabling underwater robots to maintain stable contact with offshore structures in challenging conditions,” Morrison said.
“If successful, the technology could transform offshore wind maintenance, potentially reducing fuel consumption of maintenance missions by up to 97% – from 7,000 litres per day to just 200 litres.”
Heriot-Watt University professor of robotics Yvan Petillot said the trials are focused on subsea inspection and manipulation in environments “where existing solutions cannot be used”.
Dutch geoservices firm Fugro and underwater software developer Frontier Robotics are also collaborating on the project, alongside Imperial College London.
Solving the ‘chicken head problem’
The researchers hope that autonomous underwater robots could eventually perform a wide rage of essential maintenance tasks on wind turbines.
To help robots complete tasks like repairing defects, conducting visual inspections and cleaning structures, the project aims to solve the “chicken head problem”.
This refers to the challenge of keeping a robot’s arm or tool steady against the structure against the force of waves and currents.
To overcome this, the researchers are developing advanced control systems and machine learning algorithms to allow the robots to react in real-time to changing conditions.
The UNITE researchers are also advancing 3D mapping capabilities, helping robots to navigate complex subsea structures and identify components in need of attention.
With more than 2,600 operational offshore wind turbines in the UK, and plans to quadruple capacity by 2030, demand for more efficient maintenance is set to grow.
Frontier Robotics chief executive Jonatan Scharff Willners said AI has a role to play in meeting that demand.
“With the exponential growth of offshore infrastructure, we need to look towards deploying more AI, robots and autonomy to enable the industry to take advantage of new technologies to work even more efficiently and to scale with the global demand,” he said.
Recommended for you
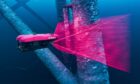