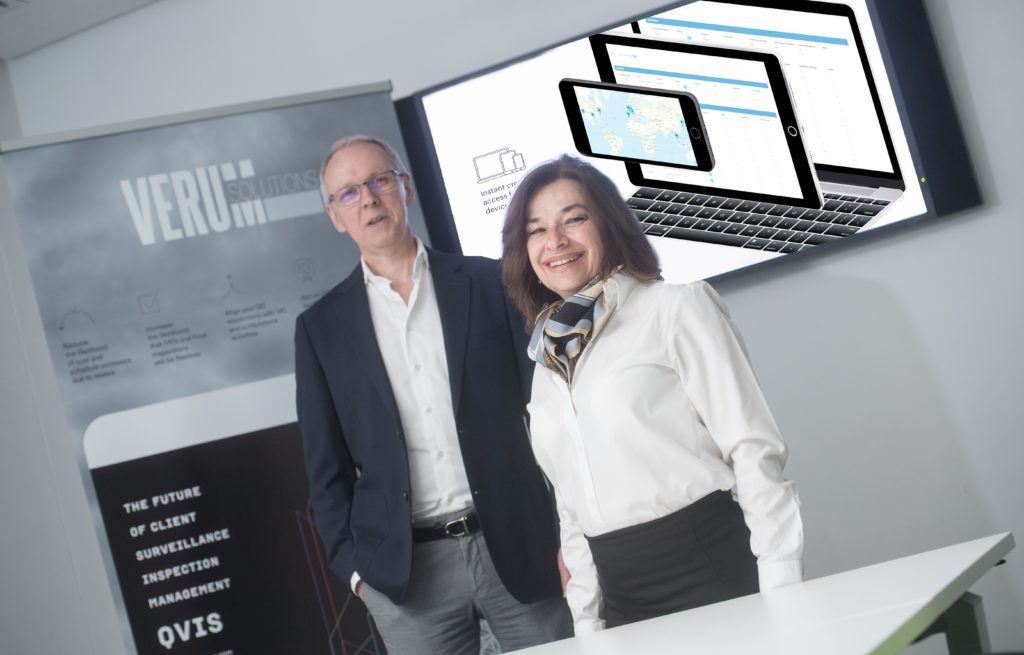
With the 30th anniversary of Piper Alpha upon us, the oil and gas industry deserves credit for its response to the tragedy and the way health and safety measures have been improved to protect the workforce.
Since 1988, we have gained a better understanding of the behaviours that cause accidents in the workplace, both on and offshore, and have adapted our management strategies accordingly.
We can now demonstrate a direct relationship between efforts taken to prevent accidents (leading indicators) and the frequency and severity of those accidents that do occur (trailing indicators). There is also significant collaboration between operators and contractors to achieve their common objective of zero incidents; built on a foundation of transparency and mutual trust.
As a result, the North Sea is often viewed as the global benchmark for HSE and technical excellence – but when it comes to quality control (QC), there’s no clear collaboration and significant mistrust.
While other management practices have evolved greatly and successfully driven HSE incident rates down, the overriding strategy to manage QC on projects has remained static over several decades.
Our management of QC during the crucial development phase has traditionally relied on the inspection and test plan (ITP). Discipline professionals fervently mark up each ITP with ‘hold’ and ‘witness’ points, and the more activities they annotate, the more comfort we take that all will be well.
This means of assuring quality has not served the industry well in the past. We continue to see similar quality failures during the engineering and build phase of new projects that significantly impact costs and schedules and, on occasion, reputations.
One technological solution developed by Verum Solutions, called Qvis, presents an opportunity to learn from the successes achieved in managing HSE, and we can use these learnings to drive down the frequency and impact of quality failures to minimise future cost and schedule overruns.
This cloud-based technology gathers inspection data, analyses it, and presents a dashboard overview of the QC performance of all project vendors and construction contractors in real time.
While parties typically strive to deliver a successful project with respect to cost and schedule, this rarely manifests in collaboration during execution. Rather, due to a lack of transparency, there is no foundation for trust and the contracting parties frequently retreat into opposing camps.
This lack of trust has a price and often results in conflict and multi-party attendance at vendors and construction sites driven by the ITP. Unfortunately, the data gathered from these inspections has minimal value in determining whether manufacturing and construction processes are under control.
For instance, delays are regularly experienced with the delivery of materials and packaged equipment due to unforeseen quality or regulatory issues, or mechanical completion and commissioning activities are disrupted because prior construction work has not been completed correctly.
By focusing our resources on those inspections that will provide data on QC leading indicators, however, we can visualise and predict where quality problems are likely to manifest before there is an impact on costs or schedule.
This allows us to engage vendors and contractors with data that substantiates our concerns and initiate and track the effect of corrective actions. Importantly, Qvis provides the data early in the manufacturing and construction cycle, which minimises disruption and provides greater assurance that delivered equipment and constructed systems will be flawless.
As Qvis technology is access right driven, the data gathered can be viewed by interested parties providing a solid foundation for reducing inspection costs through developing a transparent and trust-based relationship.
In this way, greater visibility can lead to better informed decision-making and support the recovery across the industry through increased quality during project execution and reduced downtime.
While great strides have been taken towards improving workers’ conditions across the industry, particularly in the North Sea, quality still impacts and informs health and safety processes in a major way. If we don’t act decisively to improve quality management, we run the risk of undoing some of the positive work done over the past thirty years.
Paul Milligan is the founder and CEO of Verum Solutions, which has operations in Glasgow and Monaco. He is a QA/QC specialist with over 30 years’ experience, having worked for various major operators and EPC contractors in diverse locations worldwide.
Recommended for you
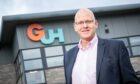