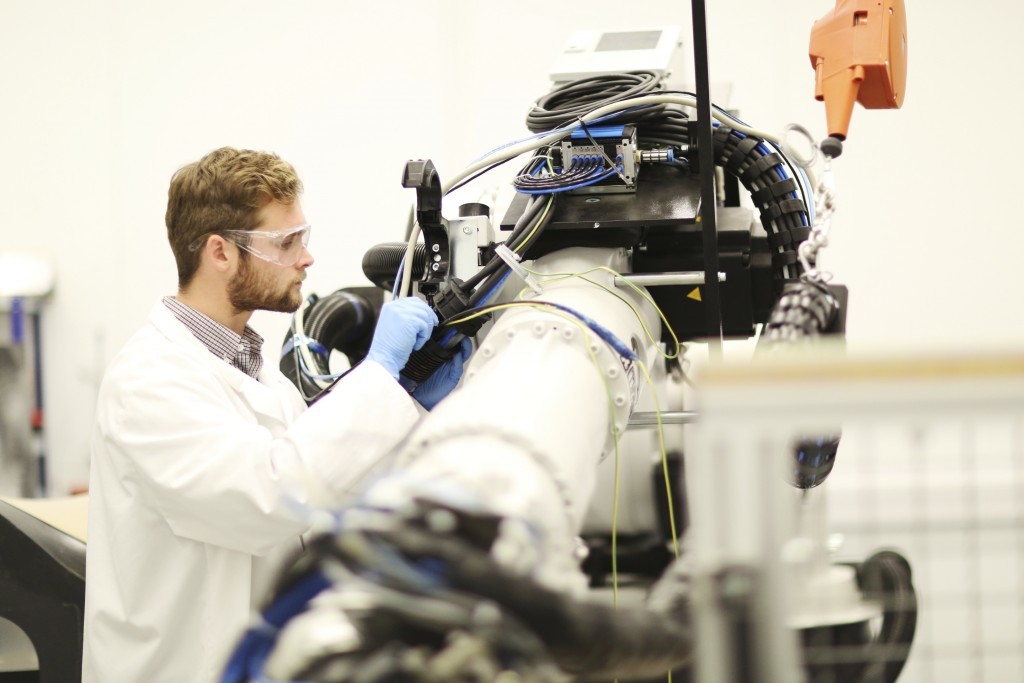
An oil rig made primarily of carbon fibre sounds far fetched, but then, who’d have thought 20 years ago that airliners could be made from the “black stuff”?
New planes such as the Boeing 787 and the Airbus A350 are already flying across the world, cutting fuel consumption and weighing a fraction of what previous generations of airliners did.
Composite technology has been around for a long time – aerospace, Formula 1, even tennis racquets have become stronger, faster and lighter – thanks to the use of new materials and applications.
The obvious appeal of developing products that could outperform and outlast existing technologies, in the extreme conditions frequently encountered in the oil and gas sector in particular is building momentum, according to a UK composite technology expert.
The National Composites Centre, based in Bristol, has been established as a centre of excellence where innovation and knowledge sharing between industry and academia are moving forward the design, manufacture and application of composites.
Graham Harrison, oil and gas lead at NCC, said the technology was progressing quickly and inquiries from the oil and gas industry had increased substantially in the last 12 months, at precisely the time that oil prices have crashed and companies examine ways to cut costs and improve performance.
In the energy sector, the boom in composites applications has yet to happen but the technology has improved significantly in recent years in areas such as composite pipe work and fluid handling.
In the North Sea, a composite drilling riser in Statoil’s Heidrun oil field has been in service since 2001.
The NCC recently commissioned a flexible oil and gas pipe test rig funded by Shell. This can test to a new standard being developed by DNV-GL which could result in a massive increase of the use of composites in this sector.
“We’re not quite at the stage of building a carbon fibre oil rig as steel is still an excellent material in many applications, but we could see composites playing a far bigger role in offshore construction as the technology progresses,” said Harrison.
“At present, glass reinforced plastic is widely used. Composites are used in a number of applications such as pipes, tanks, cable insulation and blow out preventers.”
Harrison explained: “The high cost to replace steel piping in retrofit applications and increased longevity in new construction are driving the use of composites, which withstand the severe conditions experienced in offshore environment.”
“As oil exploration has gone deeper and deeper the stress on steel structures has become immense – meaning equipment needs to be made bigger and stronger to fulfil its function and the cost of shipping and installation also begins to get expensive.
“At 3,000 metres, a riser could weigh up to 1,000 tonnes which requires large (and very expensive) rigs and ships to support this weight.”
“Composites can be designed and built to be extremely strong but also much lighter than steel. They are also corrosion resistant.”
Non-metallic materials in oilfield engineering comprise primarily composites, thermoset resins, thermoplastics and elastomers, alongside ceramics and high performance glass.
The set-up of the National Composites Centre was a £25m investment supported by the European Regional Development Fund, the South West Regional Development Agency, and the Department for Business, Innovation and Skills. It also receives £9m from the European Regional Development Fund (ERDF).
Since 2009 its job has been to bring together industry and academia to develop new technologies for the design and rapid manufacture of high-quality composite products.
Current members of the NCC include Airbus, Rolls Royce, Quinetiq and GE, Shell and Subsea 7.
Harrison believes the use of composites is set to take off.
He said: “We’re now flying in planes that have carbon fibre wings, the automotive industry is about to start using carbon fibre in anger and it will play a bigger role in the aerospace sector in coming years.
“The applications in oil and gas and other energy systems have enormous potential.”